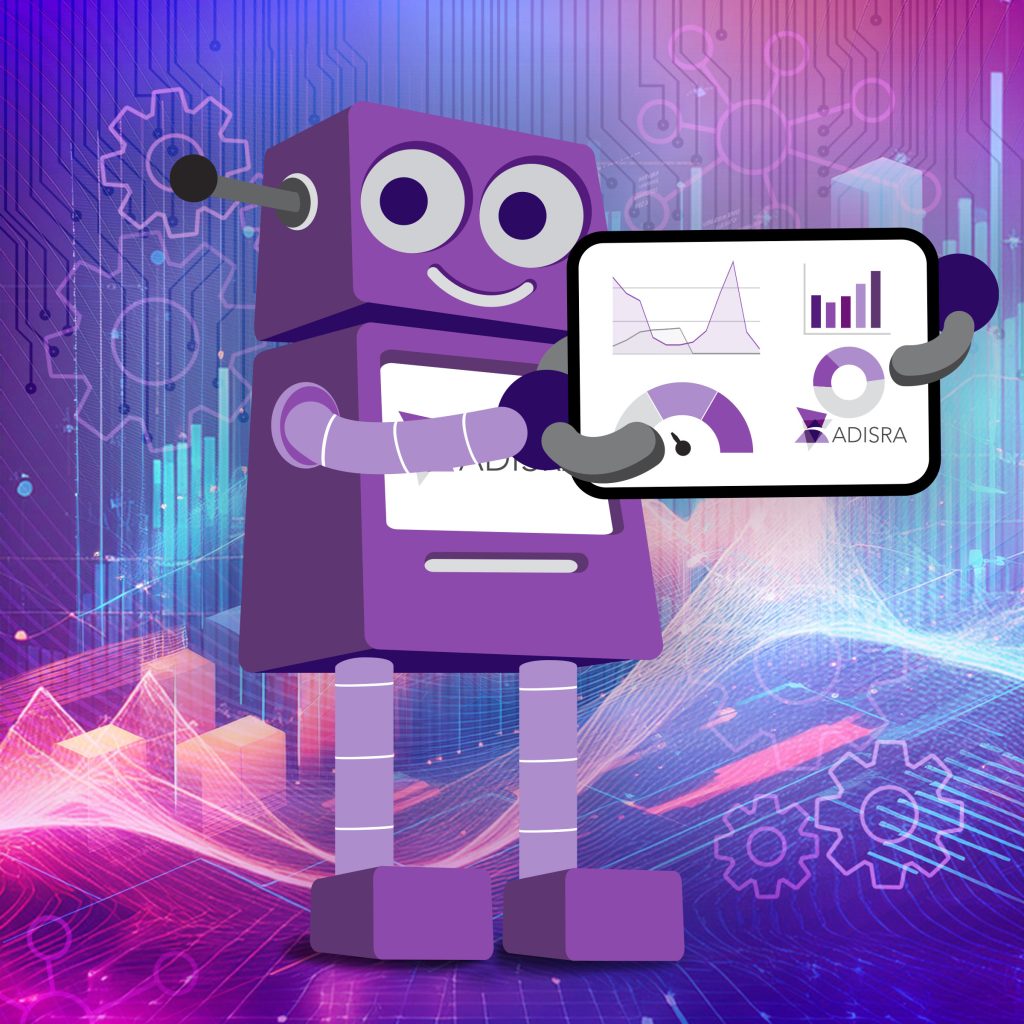
As I sorted through my countless emails this morning, I started thinking about the sheer amount of data generated daily. Email, as a primary mode of communication in today’s digital world, contributes significantly to this ever-growing data pool. It made me wonder—just how much data is created daily. And what portion of that comes from industrial sources, being generated, analyzed, and utilized? These questions inspired me to delve deeper, leading to the insights shared in this blog.
According to a report by Statista on November 21, 2024, the total volume of data created, captured, copied, and consumed globally is expected to rise sharply, reaching 149 zettabytes in 2024. Over the next five years, this figure will soar to more than 394 zettabytes by 2028. Similarly, a report from ABI Research dated July 25, 2024, highlights that industrial enterprises worldwide are forecast to generate 4.4 zettabytes (ZB) of data by 2030, up from 1.9 petabytes in 2023, with a Compound Annual Growth Rate (CAGR) of 11.1%. Most of this data is anticipated to come from discrete manufacturing (2.7 ZB by 2030), followed by the automotive sector (1.3 ZB) and process manufacturing (0.5 ZB).
One zettabyte equals 1 trillion gigabytes (GB). To put that in perspective, if your smartphone has 128 GB of storage, it would take approximately 7.8 billion smartphones to hold just one zettabyte of data. That is an astonishing amount of information! But it begs the question—are we actually utilizing all this data?
It is remarkable how little of the massive amount of data generated daily is preserved and utilized. Only 2% of the data produced and consumed in 2020 was saved and carried into 2021 according to Statista. In industrial sectors, the retention rate is slightly higher due to the critical need for real-time monitoring and automation. However, even in these settings, studies indicate that less than 10% of generated data is fully analyzed and utilized. Even so, a significant amount of industrial data remains underutilized. This gap often stems from challenges like data overload, siloed systems, limited infrastructure, and the difficulty of identifying relevant information within the noise. Overcoming these obstacles opens the door for software like ADISRA’s solutions to unlock valuable insights from this untapped resource. Later in this blog, we will explore how these tools can bridge the gap and unlock valuable insights.
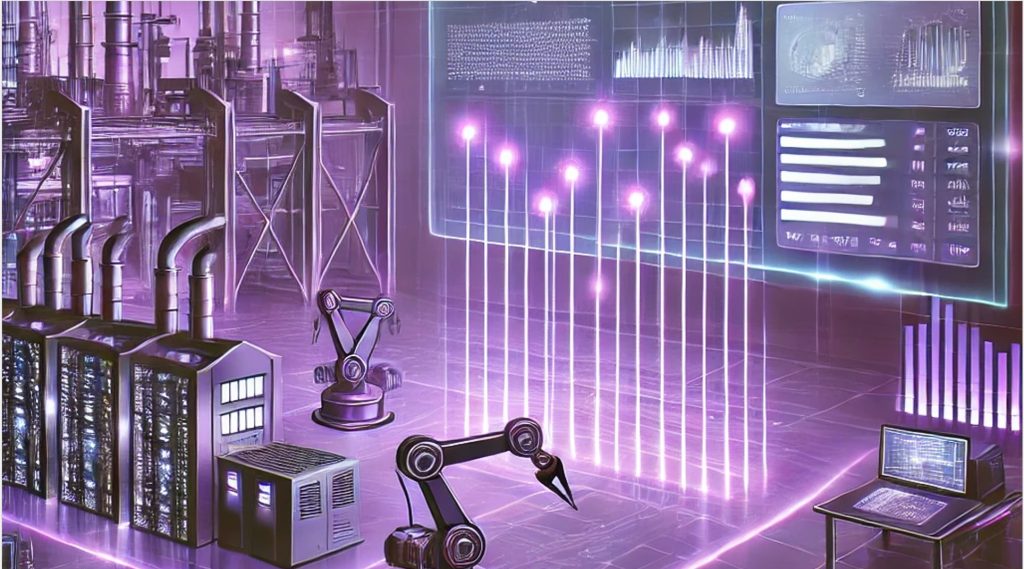
AI-Generated Graphics
What is Industrial Data?
Industrial data refers to the immense volume of information generated, collected, and utilized within industrial environments, including manufacturing, energy, transportation, and utilities. This data originates from various sources such as machines, sensors, control systems, and operational processes. It provides critical insights into equipment performance, production efficiency, energy usage, and overall operational health. Below are some sources of industrial data:
Sensors are fundamental to industrial data collection. They act as a factory’s nervous system, continuously gathering information about various aspects of the operation. Sensors allow us to ‘see’ inside complex processes, ensuring safety, efficiency, and optimal performance. Depending on the specific application and environment, sensors come in various shapes, sizes, and technologies.
Machines and Equipment. Unlike sensors, which provide individual measurements, machines often have built-in systems that record a wider range of information about their operation. Some common ways industrial machines and equipment generate data are with embedded systems, programmable logic controllers (PLCs), Computer Numeric Control (CNC) machines, Human Machine Interface (HMI), and Supervisory Control and Data Acquisition (SCADA).
Control systems act as the brains of the operation, taking in data from sensors and machines, making decisions based on pre-set logic, and sending commands to actuators to influence the physical process. Control systems constantly generate data about their operation, such as setpoints and actual values of process variables, control actions taken, alarms, events, historical trends, and operator inputs.
Production Lines are where raw materials are transformed into finished goods through a series of steps, each adding value along the way. Each stage of a production line is a potential source of valuable data such as throughput, cycle time, downtime, work-in-process (WIP), and defect rate. By tracking and analyzing these metrics, manufacturers can identify bottlenecks, optimize production flow, reduce downtime, improve quality, and boost profitability.
Enterprise Systems. These software applications manage a company’s core business processes across different departments. While not directly involved in production, they hold a wealth of data that can provide essential context for industrial data analysis. Examples of enterprise systems are enterprise resource planning (ERP), manufacturing executive system (MES), customer relationship management (CRM), and supply chain management (SCM). Manufacturers can gain a much deeper understanding of their operations by combining data from enterprise systems with data from the factory floor (sensors, machines, control systems, etc.).
With this sheer volume of data generated in industrial environments, we need to understand its unique traits to derive actionable insights. To effectively manage and leverage this abundance, we must consider the key characteristics of industrial data.
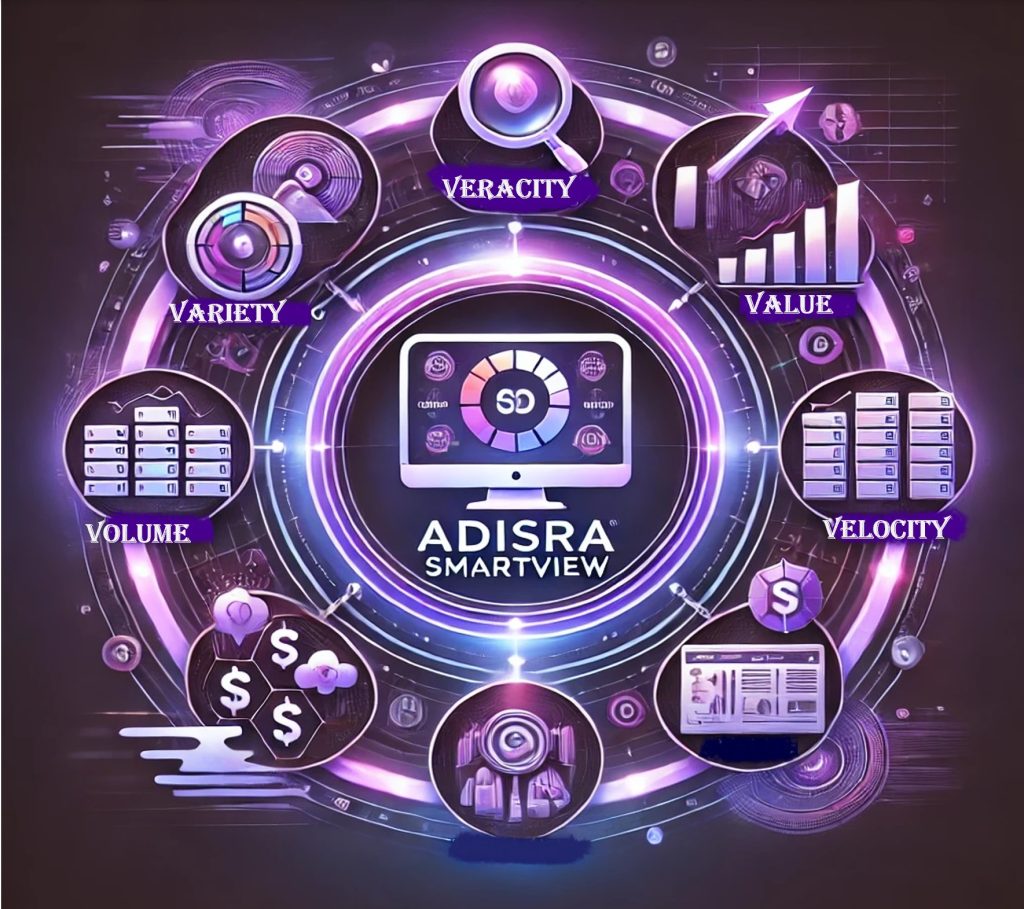
AI-Generated Graphics
Data is the lifeblood of industrial operations, driving efficiency, innovation, and decision-making. However, not all data is created equal. Industrial environments generate vast and complex datasets with unique challenges and opportunities. To harness the full potential of this data, it is crucial to understand its defining characteristics, often described as the five “V”s: Volume, Velocity, Variety, Veracity, and Value.
Volume refers to the immense quantities of data generated continuously in industrial settings, far surpassing the capacity of traditional data systems. This sheer scale presents both significant challenges and exciting opportunities. Managing such vast data demands advanced storage, processing, and analysis technologies. However, within this massive volume lies the potential for transformative insights, driving enhanced efficiency, productivity, and innovation across industrial operations.
Velocity refers to the rapid speed at which data is generated and moves through industrial systems. Unlike static datasets, industrial data arrives continuously and in real-time from multiple sources, requiring immediate attention. Its value often diminishes quickly, making real-time or near real-time analysis essential for actionable insights. Managing this high-speed data flow demands robust computing infrastructure and specialized analytics tools capable of processing continuous streams efficiently and effectively.
Variety is a defining feature that sets industrial data apart. Unlike the structured data typically found in traditional business systems, industrial data encompasses various formats, including sensor readings, machine logs, images, videos, audio recordings, and text from maintenance reports. This structured and unstructured data blend introduces significant integration, analysis, and standardization challenges. However, it also offers rich opportunities for uncovering insights across diverse data sources.
Veracity is crucial in industrial automation as it pertains to the accuracy and reliability of data. Making decisions based on inaccurate or untrustworthy data can result in costly errors, production disruptions, and safety risks. Factors such as sensor calibration issues, transmission errors, data entry mistakes, and system malfunctions can all impact data veracity. Ensuring high-quality data requires a comprehensive strategy, including rigorous data validation processes, routine sensor maintenance, robust data management systems, and consistent quality checks to build trust in the data used for critical operations.
Value represents the immense potential embedded within industrial data despite the challenges of managing it. However, this potential is not automatically realized; it must be unlocked through effective analysis and actionable insights. Data becomes truly valuable when it drives meaningful improvements in efficiency, productivity, and innovation. The extent to which industrial data delivers value depends on our ability to analyze it effectively and translate insights into tangible actions.
With this in mind, let us explore how one of ADISRA’s products can transform industrial data into actionable insights that drive positive outcomes.
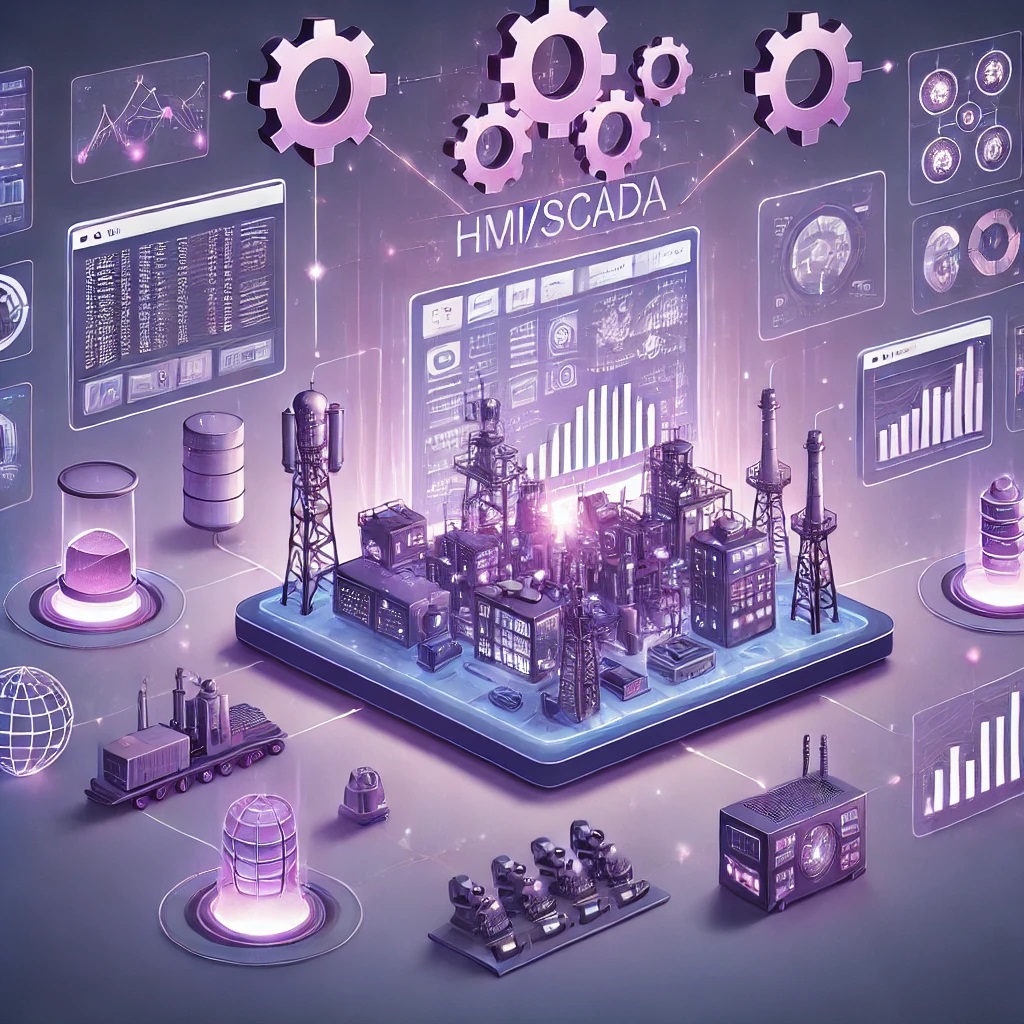
AI-Generated Graphics
ADISRA SmartView is a comprehensive HMI/SCADA package designed to process and analyze vast amounts of industrial data, enabling data-driven decisions. With an intuitive interface and robust functionality, it supports connectivity to multiple data sources and streams, offering seamless cross-platform deployment.
Beyond Traditional HMI/SCADA Functionality
ADISRA SmartView delivers all the essential features expected of a modern HMI/SCADA system, including:
- Operator dashboards
- Remote machine control
- Parameter configuration
- Alarm response
- Trending capabilities
- Recipe management
- Reporting tools
- and more.
Its built-in intelligence, powered by a rule-based expert system, sets it apart. This elevates industrial processes to a new level of automation and decision-making.
What Is a Rule-Based Expert System?
A rule-based expert system is a type of artificial intelligence that uses predefined “if-then” rules to analyze data, make recommendations, or automate actions. It operates like an expert in a specific domain, enabling smarter, faster decisions in real-time.
For example:
Rule: If the temperature is> 27°C in any zone, then activate additional cooling units.
This type of logic can be applied to various areas, such as:
- Power Usage Optimization
- Predictive Maintenance
- Alerts and Automation
- Regulatory Compliance
The components of a rule-based expert system are:
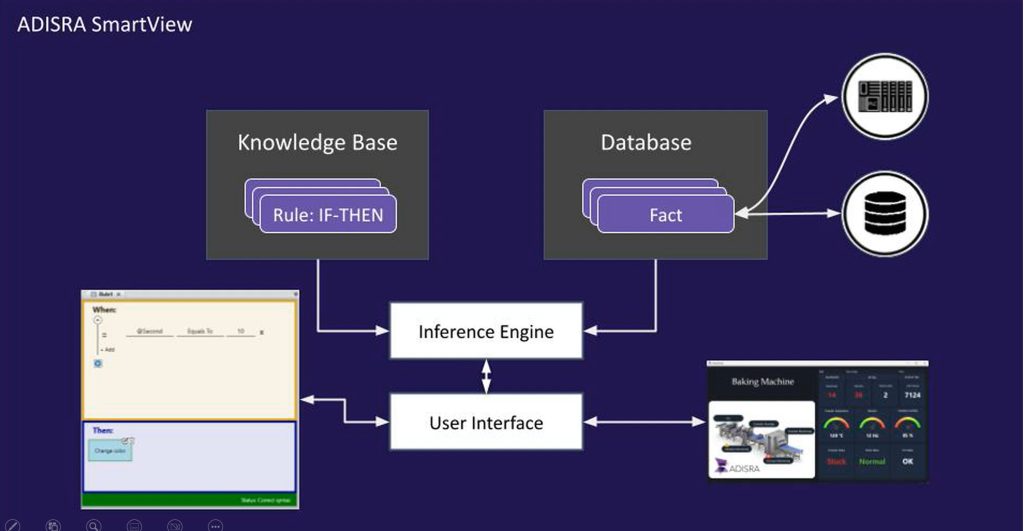
Knowledge Base is where the rules are stored.
The Inference Engine is the “thinking” part of the system. It processes the rules and compares them to real-time data or inputs.
Input/Output Interface:
Input: The system takes data from sensors or other sources.
Output: The system communicates the decision or action (e.g., a warning alert or a command to shut down equipment).
Rule-based expert systems in HMI/SCADA software bring advanced intelligence to industrial processes. Here are some real-world applications:
1. Temperature Monitoring
Scenario: Detects if equipment exceeds safe temperature limits.
Action: Shut down machinery and alert operators to prevent overheating.
2. Automated Production Line Control
Scenario: Identifies bottlenecks on conveyor belts.
Action: Adjust machine speeds to avoid disruptions.
3. Regulatory Compliance
Scenario: Monitors emissions for compliance with industry standards.
Action: Sends alerts if thresholds are exceeded.
4. Energy Efficiency Optimization
Scenario: Identifies idle equipment during non-peak hours.
Action: Automatically powers down equipment to save energy.
5. Predictive Maintenance
Scenario: Detects vibration patterns indicating bearing wear.
Action: Notifies technicians to perform maintenance before failure occurs.
ADISRA SmartView combines the power of HMI/SCADA systems with advanced rule-based intelligence, revolutionizing how real-time data can transform industrial data into actionable insights.
Experience ADISRA SmartView by downloading a software trial from our website here.
Conclusion
Harnessing industrial data empowers organizations to gain transformative insights that fuel efficiency, innovation, and competitiveness. Businesses can streamline operations, minimize waste, and boost productivity by analyzing vast amounts of real-time and historical data. This data-driven approach enables more intelligent decision-making, allowing companies to quickly adapt to changing conditions while optimizing energy usage. Additionally, leveraging industrial data strengthens safety and compliance by utilizing automated systems to proactively detect and address potential risks. Ultimately, embracing industrial data fosters agility, reduces costs, and lays the groundwork for sustainable growth in today’s increasingly data-centric landscape.