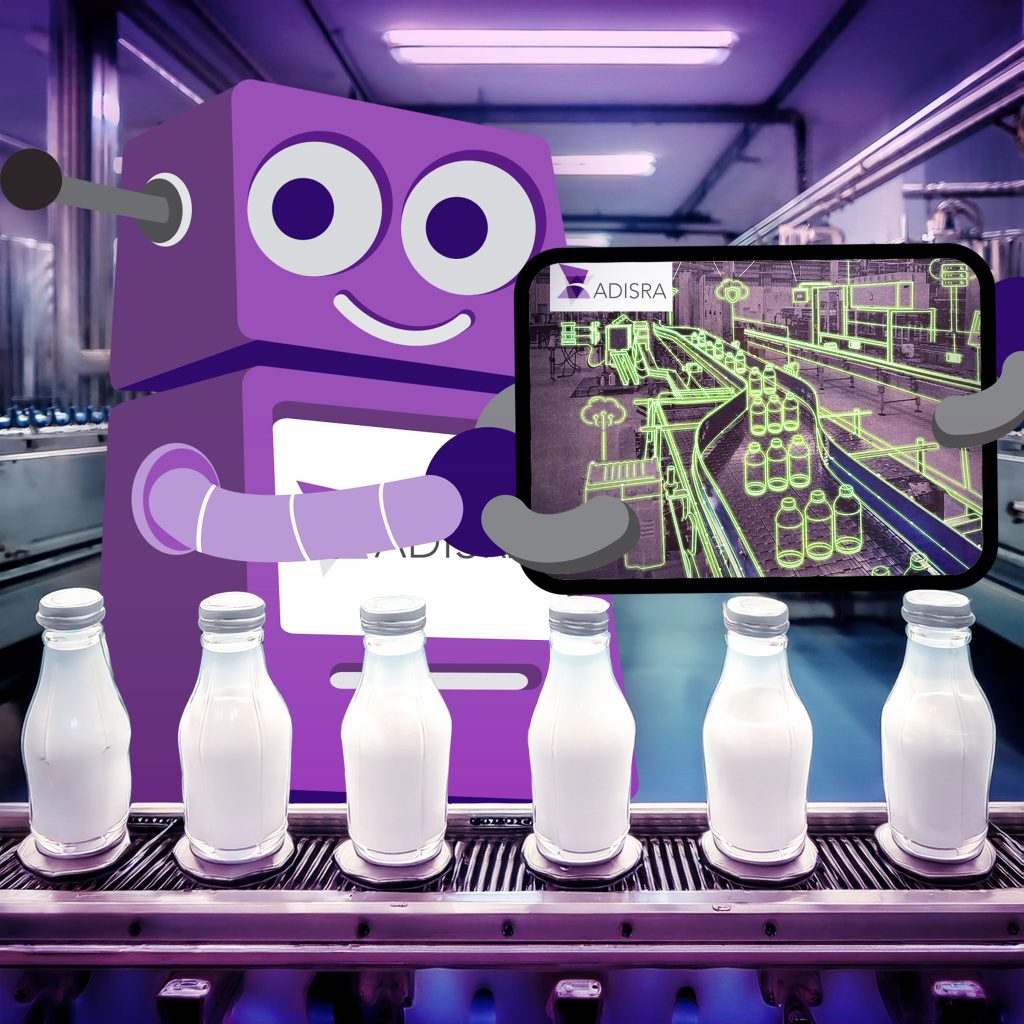
I recently came across the Coca-Cola Europacific recall from January 2025, which impacted batches of Coca-Cola, Fanta, Sprite, Minute Maid, and Fuze Tea in Belgium, Luxembourg, and the Netherlands. The recall was prompted by the detection of elevated chlorate levels in bottles and cans produced at a facility in Belgium. The affected products were identified by production codes ranging from 328 GE to 338 GE.
Chlorate, a byproduct of chlorine-based disinfectants used in water treatment, can pose potential health risks, particularly in children, by interfering with thyroid function. During routine safety checks, Coca-Cola’s bottling partner discovered the elevated chlorate levels and traced the issue back to a specific container used in the water treatment process at its Ghent production plant. Although the exact cause remains under investigation, initial findings suggest a potential malfunction or inefficiency within the plant’s water treatment system. Further analysis is ongoing to determine the precise source of the contamination and implement preventative measures.
This incident highlights the broader issue of food safety in the bottling industry and raises important questions about what preventative measures could be taken. It also made me consider the role of HMI/SCADA software in preventing such recalls by enabling real-time monitoring, early detection of anomalies, and automated safety compliance.
While the exact details of this case are still unfolding, several possible factors may have contributed to the issue. A malfunction or inefficiency in the water treatment process at the Ghent facility could have led to higher chlorate levels. Contamination from external sources, such as the municipal water supply, is another possibility. Additionally, improper cleaning and sterilization procedures within the manufacturing process may have exacerbated the problem. Regardless of the root cause, this incident underscores the critical need for rigorous quality control at every stage of production to ensure consumer safety and maintain trust in the industry.
While water treatment plays a crucial role in ensuring product safety, my focus here is on the bottling process itself—how contamination risks can be mitigated during production and how HMI/SCADA technology can help enhance quality control, detect anomalies, and prevent recalls.
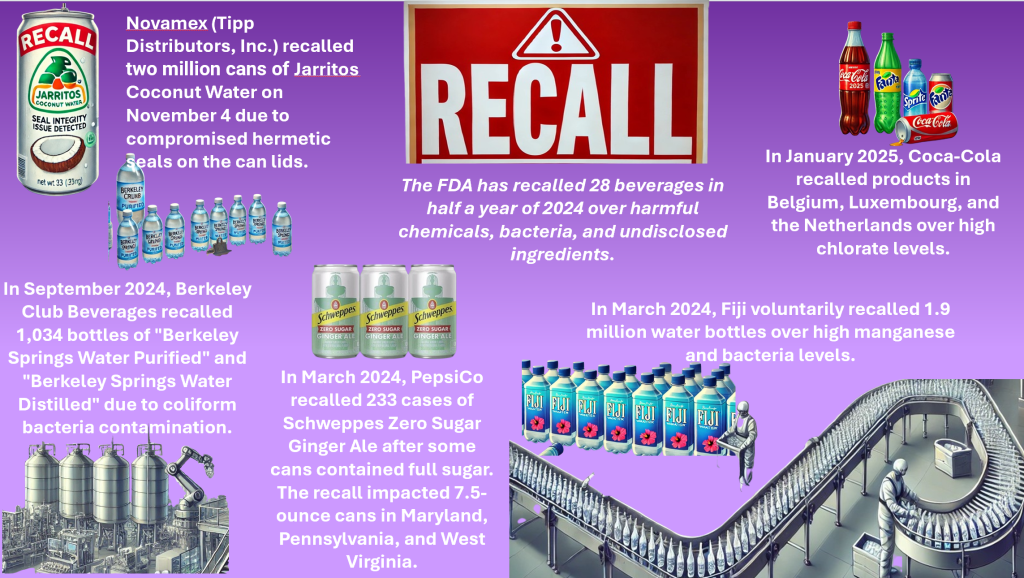
Enhancing Bottling Operations with HMI/SCADA: A Step-by-Step Breakdown
Having visited a couple of bottling plants in the past, I recall the high-level bottling process following these key stages:
1. Cleaning and Sterilization
Before filling, bottles and cans undergo thorough cleaning and sterilization to remove contaminants that could compromise product quality and safety.
HMI/SCADA software plays a vital role in monitoring and data logging throughout this process. It continuously records key parameters, ensuring the cleaning and sterilization cycles are effective and meet safety standards.
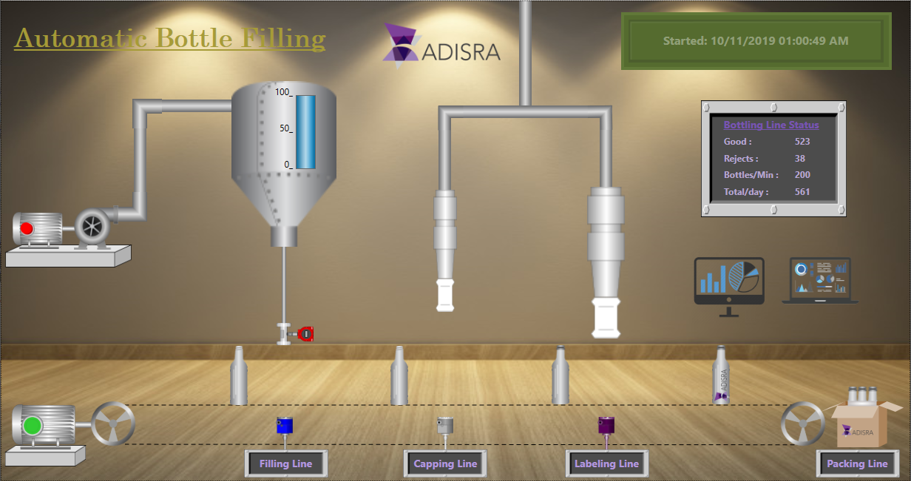
2. Filling
Once cleaned, the containers are filled with the beverage. This step ensures the correct fill level and minimizes headspace (the space at the top of the container), directly impacting product quality, shelf life, and integrity.
HMI/SCADA software optimizes and controls the filling process by managing:
– Fill-level monitoring to ensure accuracy and consistency.
– Flow rate control to prevent overfilling or underfilling.
– Filling cycle management for efficiency and precision.
– Alarm management, data logging, and reporting to track deviations and ensure compliance.
For example, in flow rate control, HMI/SCADA software continuously monitors and adjusts the liquid flow rate, maintaining consistency and preventing fluctuations that could affect product quality.
3. Capping or Sealing
After filling, bottles and cans are securely sealed to prevent leaks, maintain freshness, and protect against contamination. Proper capping ensures product integrity during storage and distribution.
HMI/SCADA systems enhance this step by providing:
– Capping torque control to ensure consistent torque levels.
– Capping cycle management for efficiency and reliability.
– Cap inspection and rejection to detect faulty seals.
– Alarming, data logging, and reporting for quality control.
For instance, torque sensors integrated with capping machines, monitored through HMI/SCADA software, ensure caps are applied with the correct force—preventing under-torque issues (leading to leaks) and over-torque problems (causing cap or bottle damage).
4. Labeling
Labels provide essential product information, ensuring proper identification and aiding consumer decision-making. This stage requires precision to ensure correct placement and alignment.
HMI/SCADA software supports:
– Label placement and alignment control for accuracy.
– Label application speed control to maintain consistency.
– Label inspection and rejection using vision systems.
– Label inventory management for efficient stock control.
– Data logging and reporting for traceability.
For example, vision systems equipped with cameras and image processing algorithms can inspect bottles in real time, detecting defects or misaligned labels. HMI/SCADA software processes these insights, allowing operators to make immediate adjustments or reject faulty bottles—eliminating the need for manual inspection.
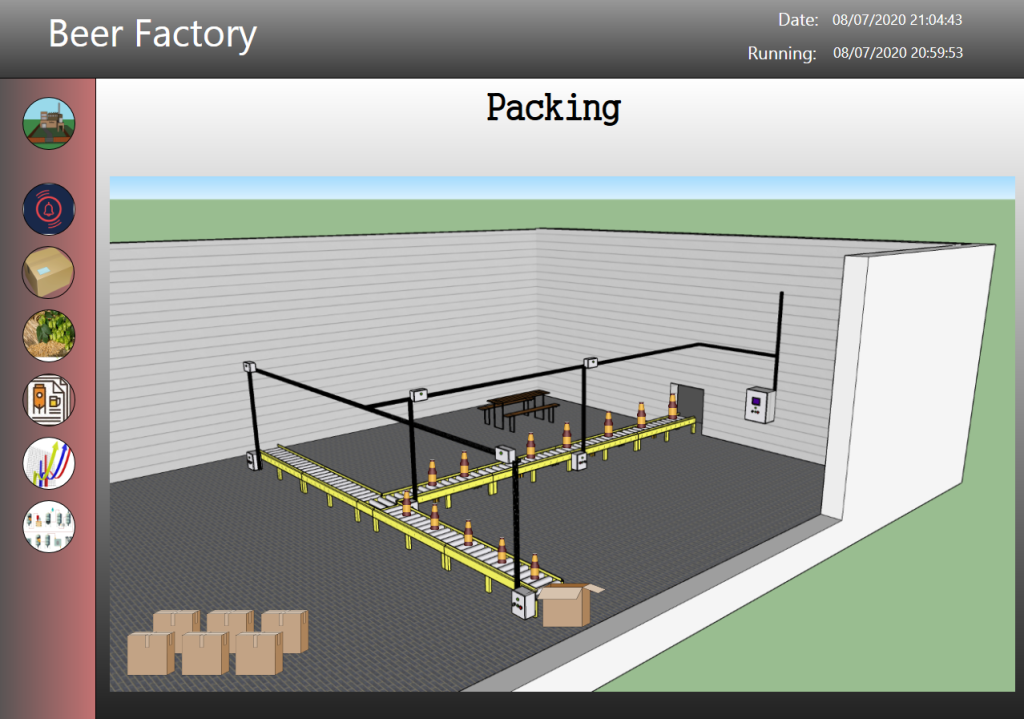
5. Packaging and Distribution
The final stage involves grouping and securing bottled products for transportation, ensuring they arrive safely at retail outlets or distribution centers.
HMI/SCADA software can assist in:
– Pallet loading optimization for balanced weight distribution.
– Packaging line monitoring and control to ensure efficiency.
– Inventory management for real-time stock tracking.
– Distribution routing optimization to improve logistics.
– Data logging, alarming, and reporting for quality assurance.
For instance, weight distribution monitoring ensures that products are evenly placed on pallets, preventing instability and potential damage during transit. HMI/SCADA systems integrate with load sensors to provide real-time weight data, allowing operators to make necessary adjustments for a balanced load.
Each of these steps involves further complexities depending on the specific product, liquid type, cap design, and packaging requirements. However, the integration of HMI/SCADA technology enhances automation, quality control, and efficiency, ultimately reducing risks and improving overall bottling operations.
Optimizing Bottling Operations with ADISRA SmartView
With ADISRA SmartView, the system provided real-time alerts when a filling station’s nozzle pressure dropped by 20%, increasing cycle time by five seconds. The line supervisor was immediately notified and could dispatch a technician to replace the faulty nozzle before it caused significant slowdowns. This proactive approach prevented bottlenecks in later stages of production, avoiding a complete line shutdown due to a critical failure.
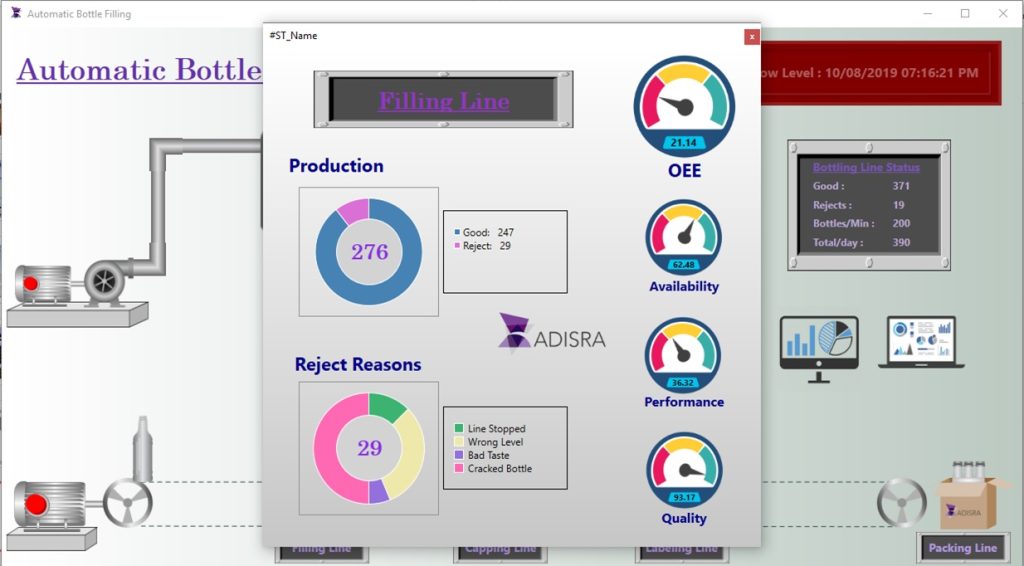
By leveraging ADISRA SmartView rule-based expert system the system is able to detect anomaly by continuously monitored sensor data, identifying issues like declining nozzle pressure or signs of wear in bottling machinery. This transformed the plant’s operational strategy from an “inspect and reject” model to a proactive “predict and prevent” approach—minimizing downtime, improving efficiency, and maintaining product quality.
With ADISRA SmartView, bottling plants gain real-time insights, automated alerts, and rapid diagnostics, helping to prevent machine malfunctions before they impact production. This level of intelligence enhances predictive maintenance, reduces waste, and ensures seamless, high-quality bottling operations.
Are you ready to try ADISRA SmartView? Download our software here.
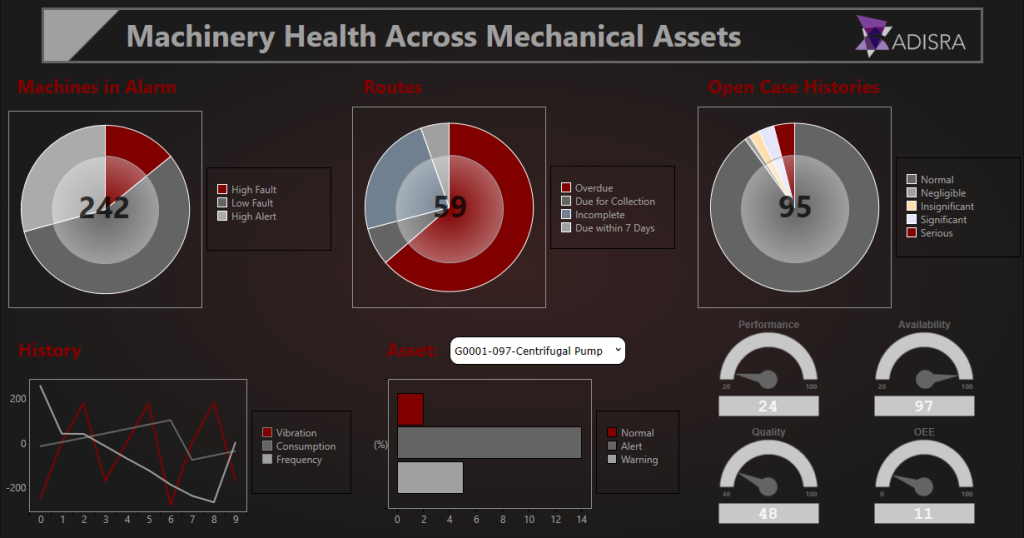
Ensuring Compliance with FDA 21 CFR Part 11 in Bottling Operations
For beverage manufacturers operating in regulated markets, compliance with FDA 21 CFR Part 11 is essential. This regulation establishes requirements for electronic records and electronic signatures, ensuring data integrity, traceability, and security in automated systems. ADISRA SmartView supports compliance by providing secure audit trails, user authentication, and electronic signatures, enabling bottling plants to track changes, verify actions, and maintain regulatory documentation seamlessly. By integrating real-time monitoring, data logging, and automated reporting, ADISRA SmartView helps manufacturers uphold food safety standards while optimizing operational efficiency.
For more details on ADISRA SmartView and its compliance with FDA 21 CFR Part 11, check out the following blog on this standard and find a link below to the documentation covering this feature.
Conclusion: Strengthening Food Safety and Efficiency in Bottling with ADISRA SmartView
The Coca-Cola Europacific recall serves as a stark reminder of the importance of rigorous quality control in the bottling industry. While contamination risks can originate from multiple sources, bottling facilities must implement robust real-time monitoring, automated alerts, and predictive maintenance to prevent product recalls and ensure consumer safety.
With ADISRA SmartView, manufacturers can move from a reactive approach to a proactive strategy, leveraging HMI/SCADA technology and rule-based expert systems to detect anomalies, optimize production processes, and maintain compliance with strict regulatory standards like FDA 21 CFR Part 11. ADISRA SmartView empowers bottling plants with real-time insights, anomaly detection, and automated decision-making, ensuring seamless and efficient operations from cleaning and sterilization to filling, capping, labeling, and distribution.
By integrating advanced automation, artificial intelligence, analytics, and edge computing, beverage manufacturers can enhance production efficiency, minimize downtime, and maintain product quality—while safeguarding their brand reputation. As the industry continues to evolve, the adoption of intelligent monitoring systems like ADISRA SmartView will be crucial in ensuring food safety, regulatory compliance, and operational excellence.
Are you ready to take your bottling operations to the next level? Download ADISRA SmartView today and experience the power of intelligent automation.
ADISRA®, ADISRA’S logo, InsightView®, and KnowledgeView® are registered trademarks of ADISRA, LLC.
© 2025 ADISRA, LLC. All Rights Reserved.