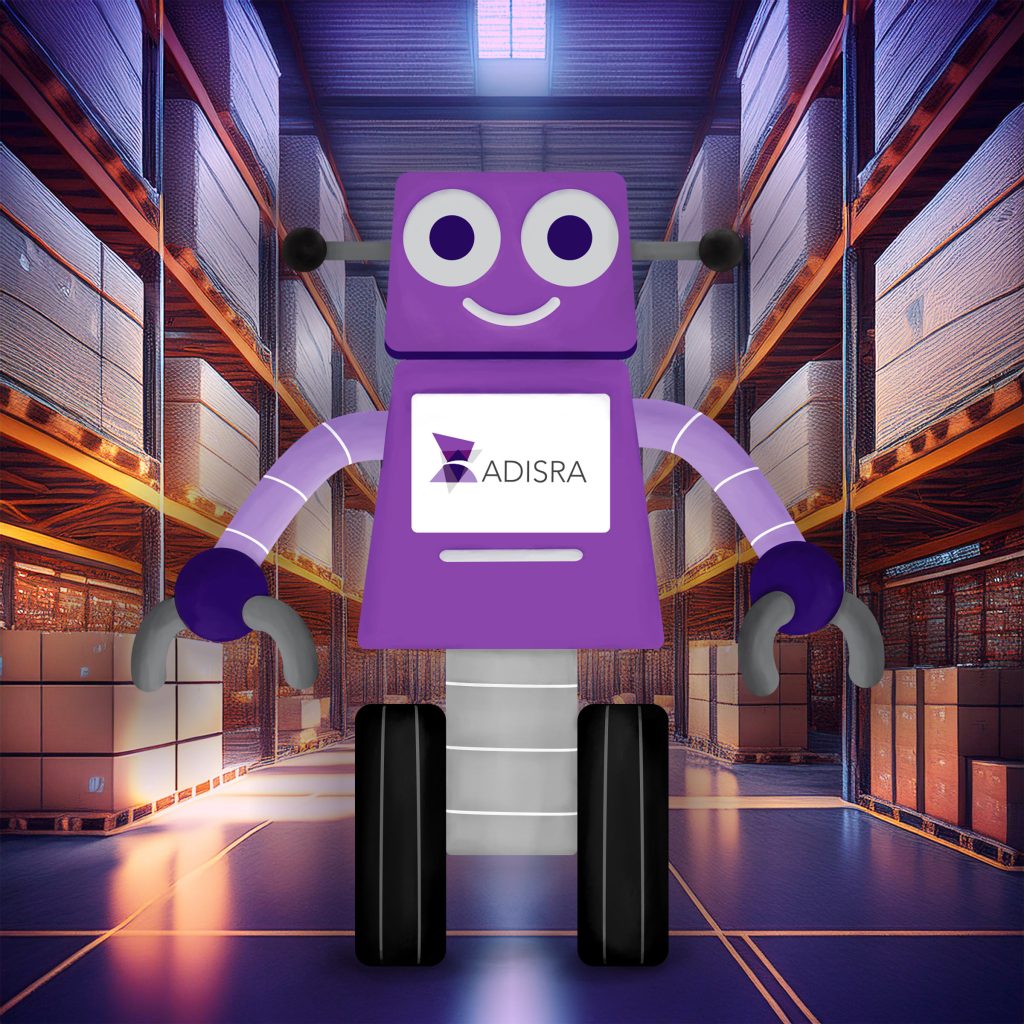
Autonomous Mobile Robots (AMRs) have become a staple in modern warehouses and clean rooms. These robots leverage advanced technologies to navigate and execute tasks without direct human control. Unlike traditional automated systems that are confined to fixed paths or preprogrammed routes, AMRs are equipped with sensors, cameras, artificial intelligence (AI), and real-time data processing capabilities. This allows them to independently understand their surroundings and make decisions on the fly, even in dynamic and complex environments.
According to Next Move Strategy Consulting, the Autonomous Mobile Robot (AMR) market was valued at USD 1.24 billion in 2023 and is projected to reach USD 3.13 billion by 2030, with a compound annual growth rate (CAGR) of 18.7%.
The number of AMRs in a typical warehouse or clean room can vary greatly based on factors such as facility size, operational complexity, and the degree of automation needed. However, most facilities deploy multiple AMRs to meet their needs. HMI/SCADA software plays a crucial role in this environment by being the centralized platform for planning, managing, and optimizing the entire AMR fleet operations.
Autonomous Mobile Robots vs. Automated Guided Vehicles: What’s the Difference?
Autonomous mobile robots (AMRs) are robotic vehicles that operate independently without requiring human control or intervention. Unlike automated guided vehicles (AGVs), which follow predefined paths, cues, or signals to perform tasks like picking up or delivering materials, AMRs can navigate dynamically and adjust their routes to avoid obstacles. AMRs are generally smaller, more flexible, and able to move freely in their environment.
In automotive plants, AGVs are commonly used to transport supplies from storage areas to assembly lines or from one station to the next, following fixed routes. Their paths and tasks are predefined, and they navigate along specific routes using floor markers, magnetic strips, or sensors embedded in the facility’s floor. AGVs are ideal for structured environments, handling repetitive tasks, and providing cost-effective solutions in operations with minimal traffic.
AMRs are ideal for dynamic environments where flexibility, scalability, and autonomous navigation are crucial. In semiconductor clean rooms, AMRs are commonly used to transport sensitive materials between sterile areas. Since clean room layouts and conditions can change due to space constraints, human workers, contamination control measures, and varying tasks, AMRs offer adaptability. They can autonomously adjust their routes to reduce movement through high-traffic areas, avoid contamination-prone zones, or steer clear of human workers, ensuring efficient and safe operation.
Rise of the Autonomous Mobile Robot
Moore’s Law states that the number of transistors in a computer doubles approximately every 18 months, resulting in exponential growth in computing power. This rapid advancement has been a key driver behind the rise of Autonomous Mobile Robots (AMRs). The availability of more powerful and affordable computing has accelerated the development of sensors, vision systems, and analytics technologies, enabling AMRs to interact with their environment in real-time and operate more intelligently and efficiently.
As computing power continues to evolve, so too does the sophistication of AMRs. These advancements have enabled the integration of artificial intelligence (AI) and machine learning algorithms into AMRs, allowing them to process vast amounts of data quickly and make autonomous decisions on the fly. This intelligence enables AMRs to adapt to complex environments, optimize their routes, and collaborate with other machines or human workers. Moreover, the decreasing cost of high-performance hardware has made these robots more accessible to industries ranging from logistics and manufacturing to healthcare, further driving their widespread adoption.
The Growing Role of Autonomous Mobile Robots (AMRs) in Modern Warehouses
The first documented online purchase was made In 1994 when a man in Philadelphia bought a compact disc, Ten Summoner’s Tales by Sting, from a company in Nashua, NH. Fast forward to 2023 where global retail e-commerce sales have reached an estimated 5.8 trillion U.S. dollars, according to Statista. This sales figure is expected to grow by 39 percent in the coming years surpassing 8 trillion U.S. dollars by 2027.
As e-commerce continues to surge, the demand for efficient warehouse and logistics management has skyrocketed, driving the rapid adoption of Autonomous Mobile Robots (AMRs). These robots, equipped with sensors, cameras, and artificial intelligence, transform warehouse operations. AMRs can navigate dynamically, adjusting their paths in real-time to accommodate changes in the warehouse layout, avoid obstacles, and adapt to unexpected situations, such as human workers or forklifts crossing their paths.
AMRs are built to work safely alongside humans, making them ideal for environments with mixed traffic. They can detect obstacles, including people, and adjust their speed or routes to prevent collisions. This capability is crucial in fast-paced, busy warehouses where constant interaction between robots and human workers is common. As the demand for faster order fulfillment grows, AMRs are increasingly important in ensuring efficiency and safety in warehouse operations.
How HMI/SCADA Software Powers Autonomous Mobile Robot (AMR) Fleet Management
HMI/SCADA software, such as ADISRA SmartView, serves as a centralized platform for managing and optimizing the operations of an Autonomous Mobile Robot (AMR) fleet. With ADISRA SmartView, operators can oversee multiple AMRs from a unified interface, providing real-time visibility into each robot’s status, location, and task progress.
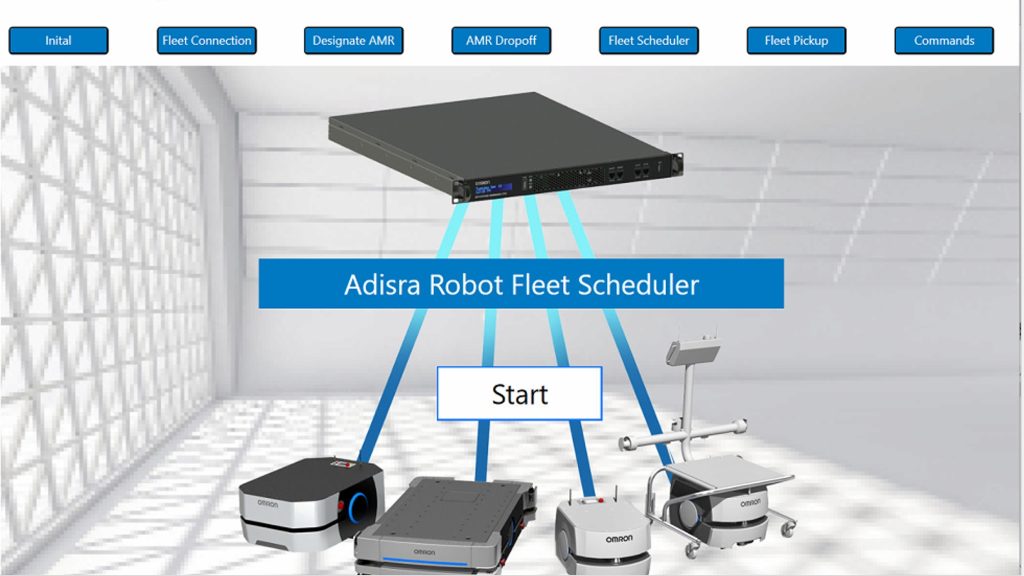
The software enables users to efficiently assign and prioritize orders ensuring smooth logistics operations. ADISRA SmartView optimizes load transport by selecting the most appropriate AMR for each task, ensuring goods are moved at the ideal time. It also offers the flexibility to modify load destinations or shift priorities as needed providing complete control over the AMR fleet and allowing for seamless adjustments in real-time.
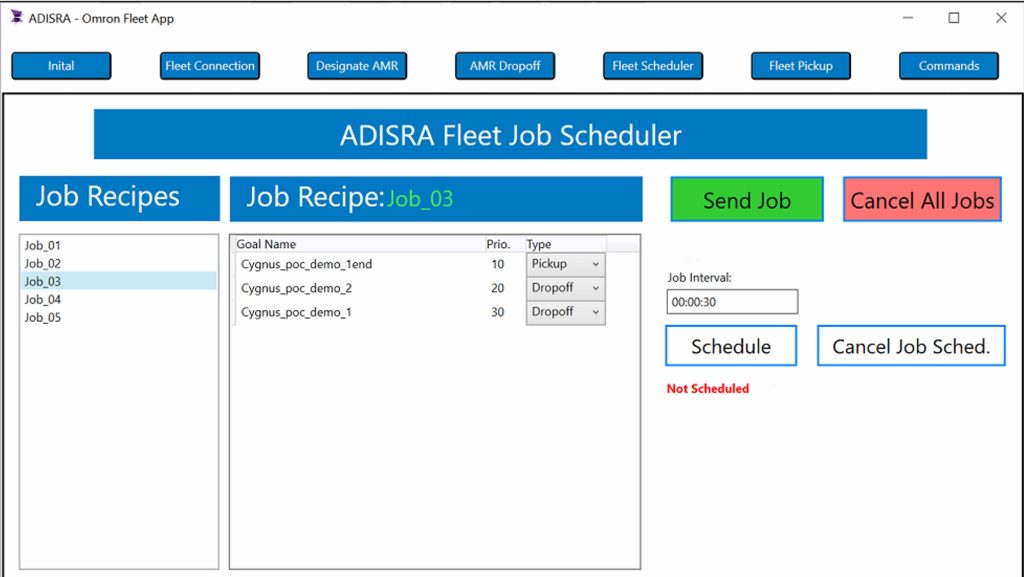
The ADISRA SmartView application offers an easy and efficient way to add or remove vehicles, modify destination stations, or adjust missions to fit your operational needs at any time. Additionally, with ADISRA SmartView’s seamless integration capabilities, it can easily connect with third-party systems like Warehouse Management Systems (WMS) or Enterprise Resource Planning (ERP) systems, enhancing overall workflow coordination and data connectivity.
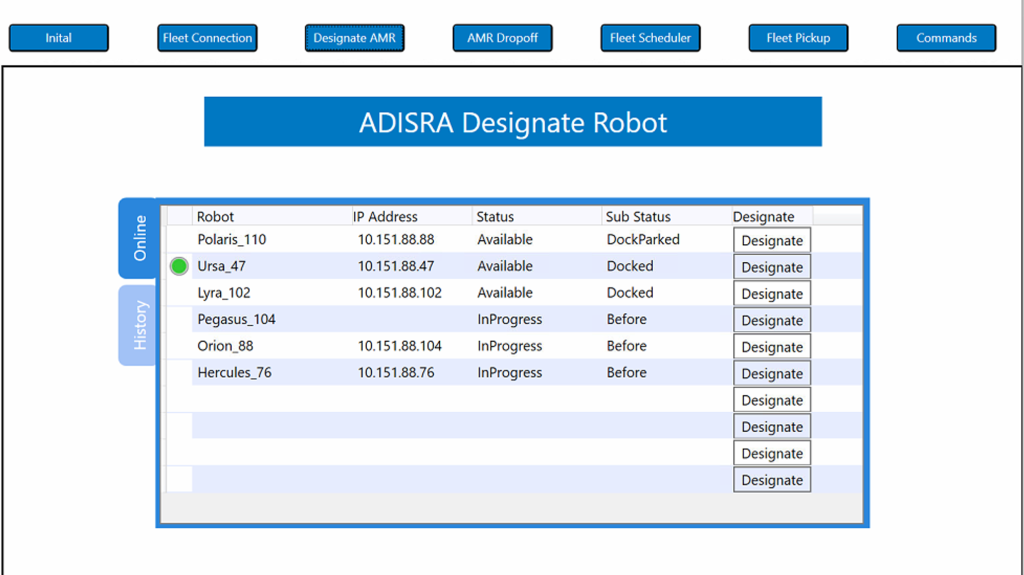
The ADISRA SmartView application plays an important role in enabling effective load balancing within an AMR fleet by providing real-time visibility and control over all robot operations. Through the centralized interface, operators can monitor the status, location, and workload of each robot, ensuring tasks are distributed evenly across the fleet. The software automatically analyzes data such as task priority, robot availability, and proximity to dynamically assign tasks and prevent any robot from being overloaded while others remain idle. This allows for better productivity and efficiency of the robots.
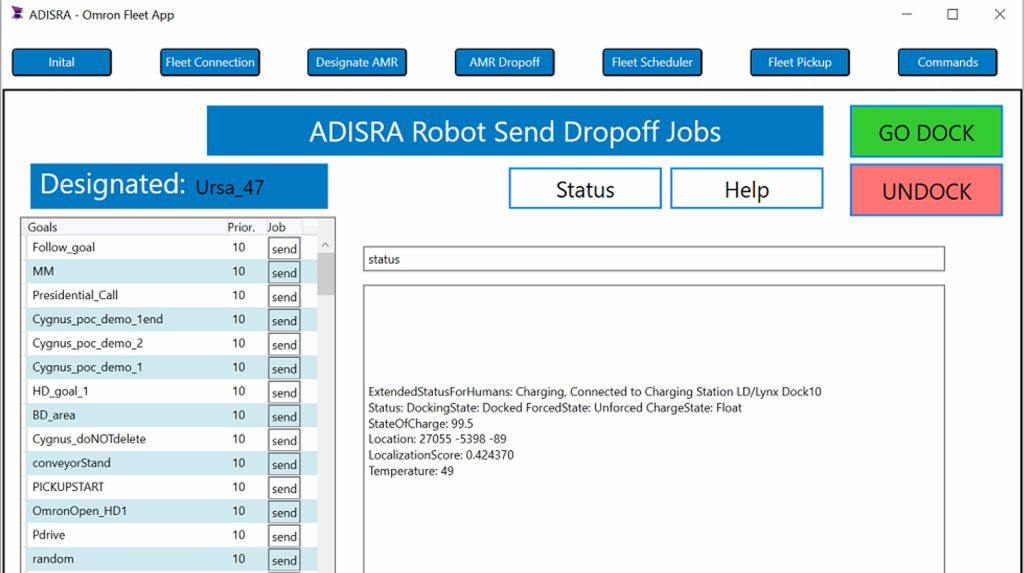
With ADISRA SmartView’s OEE capabilities, the application can be extended to deliver transparent and in-depth analytics on fleet performance. The comprehensive view of AMR system behavior allows operators to optimize performance and make informed, data-driven decisions. Additionally, with ADISRA SmartView’s built-in rule-based expert system, predictive analytics—such as monitoring battery life—can be implemented, enabling proactive maintenance and enhancing operational efficiency.
Experience ADISRA SmartView by downloading a software trial from our website here.
Conclusion
In today’s fast-paced, automated environments, effective fleet management of Autonomous Mobile Robots (AMRs) is crucial for maintaining operational efficiency. HMI/SCADA software, like ADISRA SmartView, provides a powerful solution for overseeing, managing, and optimizing AMR operations. ADISRA SmartView enables users to control their AMR fleets with flexibility and efficiency by offering real-time visibility, dynamic task assignment, and seamless integration with third-party systems such as WMS and ERP.
The advanced features, such as load balancing, predictive analytics, and the ability to adapt to changing operational demands, ensure that resources are used effectively and robots remain productive without downtime. ADISRA SmartView’s OEE capabilities further enhance its value by offering in-depth performance insights, allowing for continuous optimization and data-driven decision-making.
Incorporating HMI/SCADA software into AMR fleet management empowers organizations to streamline operations, reduce costs, and achieve greater levels of productivity, making it an essential tool for today’s automated systems.