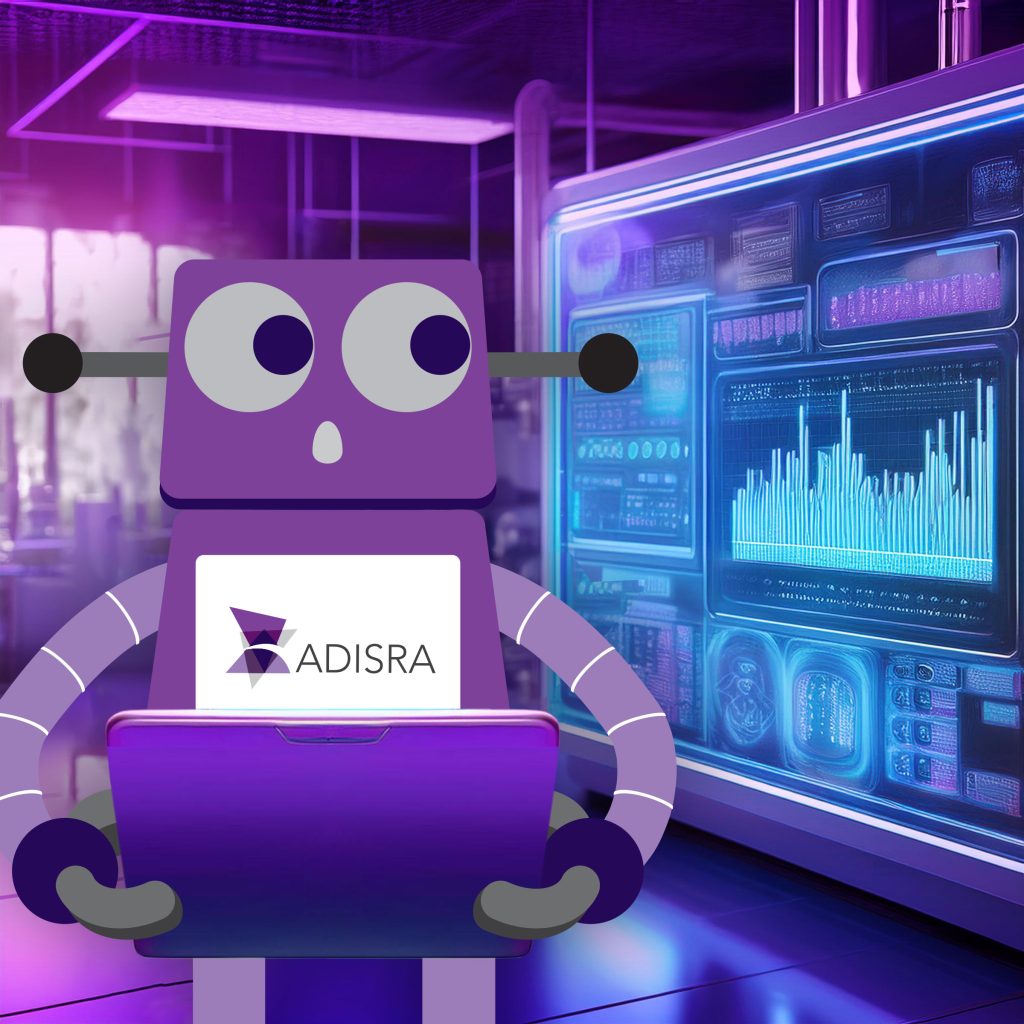
A recurring theme when speaking with customers is their drive to enhance production efficiency. The key metric in this pursuit is Overall Equipment Effectiveness (OEE), which measures the performance of equipment and manufacturing processes. Central to OEE is the concept of the “Six Major Losses,” a foundational element of Total Quality Management (TQM) and Total Productive Maintenance (TPM). These six losses represent the primary sources of inefficiency in manufacturing, directly affecting production output, quality, and costs. Understanding and addressing them is critical to achieving operational excellence.
TPM, a methodology rooted in Japan, draws heavily from American quality management principles. Influential figures like Dr. W. Edwards Deming significantly shaped its development, introducing the principles of TQM during his numerous visits to Japan.
TQM is a management philosophy focused on continuous improvement across all facets of an organization. It emphasizes exceeding customer expectations through the active involvement of every employee in ongoing refinement. Over the decades, TQM has evolved, becoming a cornerstone of modern business practices thanks to contributions from various individuals and organizations.
TQM and the Six Major Losses share a common goal: improving efficiency and reducing waste in manufacturing processes. While TQM provides a broad framework for achieving quality through continuous improvement, the Six Major Losses are focused on identifying and resolving equipment-related productivity challenges.
The Six Major Losses are a core element of TPM and highlight the key sources of productivity loss and inefficiency in manufacturing. By addressing these areas, TPM seeks to eliminate waste and optimize OEE, driving greater efficiency and effectiveness in production operations.
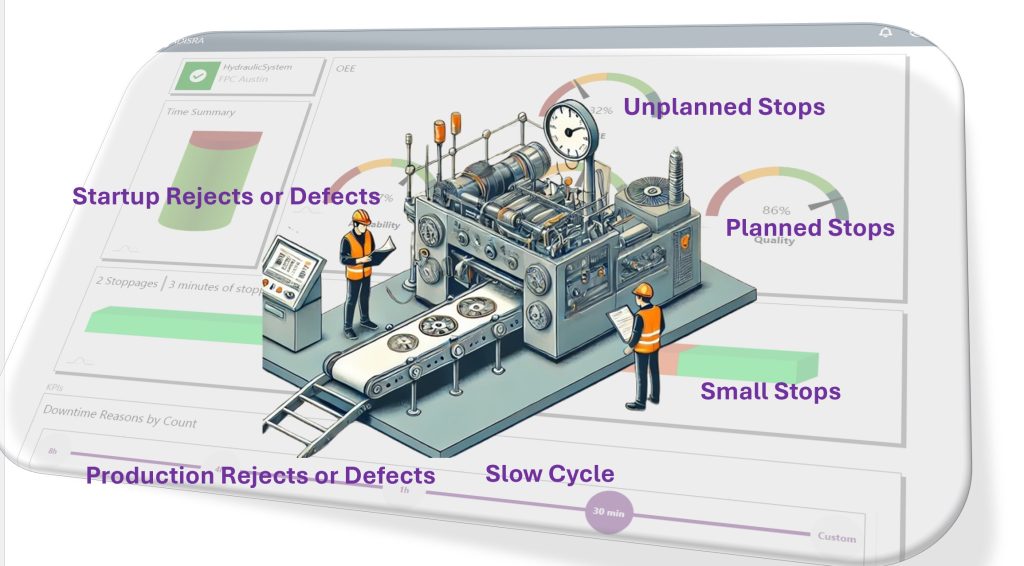
How to Calculate Availability, Performance, and Quality
OEE consists of three key parameters: availability, performance, and quality. Let’s start with availability, which measures the proportion of planned production time a machine runs. The formula is:
Availability = Run Time / Planned Production Time
For example, imagine a plant running a single shift where a machine has a planned production time of 8 hours daily. On a given day, the machine spends 1.5 hours on a setting change and 30 minutes waiting for raw materials. This means the machine was only operational for 6 of the 8 planned hours. Using the formula:
Availability = 6 hours / 8 hours = 75%
A higher availability percentage reflects better operational efficiency by minimizing unplanned downtime during production.
The second parameter of OEE is Performance, which measures how efficiently a machine operates compared to its maximum potential. It evaluates the ideal cycle time ratio to the actual cycle time. The formula for performance is:
Performance = (Ideal Cycle Time × Total Count) / Run Time
Let’s break it down with an example:
Suppose the ideal cycle time for a machine is 1.2 minutes per part. The machine was operated for 5.5 hours and produced 200 parts. Using the formula:
Actual Cycle Time = Operating Time / Number of Parts
Actual Cycle Time = (5.5 × 60 minutes) / 200 parts = 330 minutes / 200 parts = 1.65 minutes per part
Now, calculate performance:
Performance = Ideal Cycle Time / Actual Cycle Time
Performance = 1.2 minutes / 1.65 minutes = 72%
This means the machine operates at 72% of its maximum theoretical performance. A performance score of 100% indicates the machine is running at its ideal speed without any slowdowns or interruptions. However, performance accounts for “performance losses,” such as small stops, slow cycles, or other inefficiencies that reduce the machine’s speed during production.
The final parameter of OEE is Quality, which measures the proportion of good parts produced out of the total parts manufactured. For instance, out of 200 parts produced, only 170 were good, while 30 were rejected. The formula for quality is:
Quality = Good Count / Total Count
Using this formula:
Quality = 170 good parts / 200 total parts = 85%
To calculate the total OEE, we combine all three parameters:
OEE = Availability × Performance × Quality
In our example:
OEE = 0.75 × 0.72 × 0.85 = 45.9%
This means the machine is only being utilized at 45.9% efficiency, leaving 54.1% as an opportunity for improvement. This highlights the importance of OEE, as it provides an overall efficiency score and identifies specific areas for improvement.
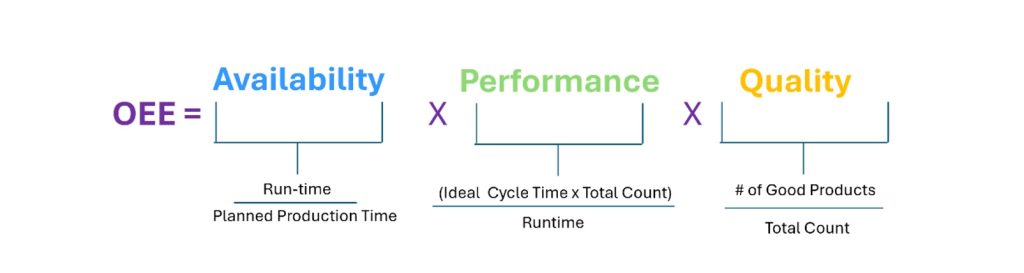
In this example, Performance is the lowest parameter, suggesting it should be the initial focus for optimization. This targeted approach allows for continuous improvement and better equipment utilization over time.
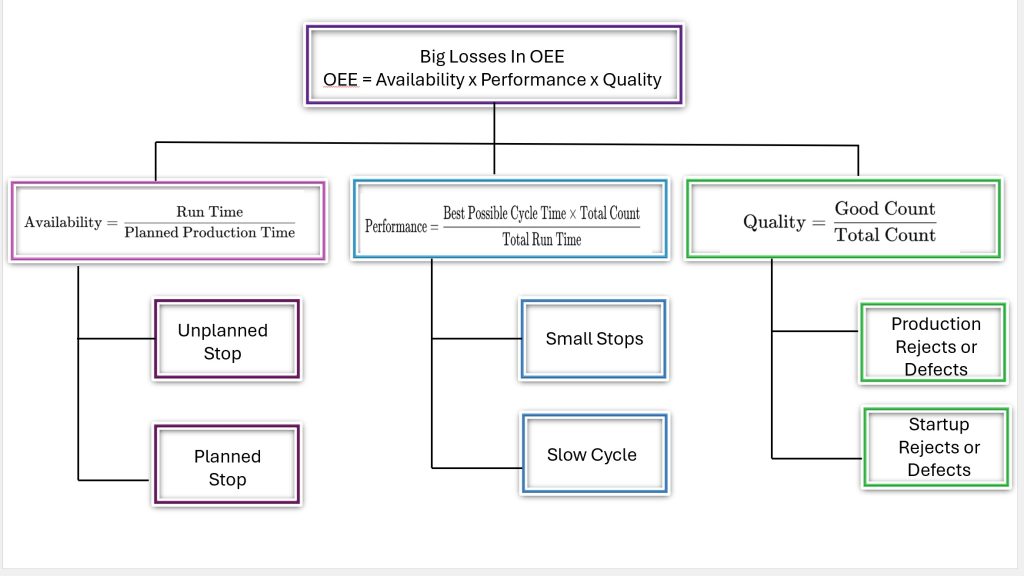
Unmasking Inefficiencies: A Deep Dive into the Six Major Losses
We define six major losses as the foundation of OEE, each affecting one of its three core parameters: Availability, Performance, and Quality. Under each parameter, two types of losses are categorized. For example, Availability includes losses from unplanned stops and setup and adjustments. Let us explore these losses in detail:
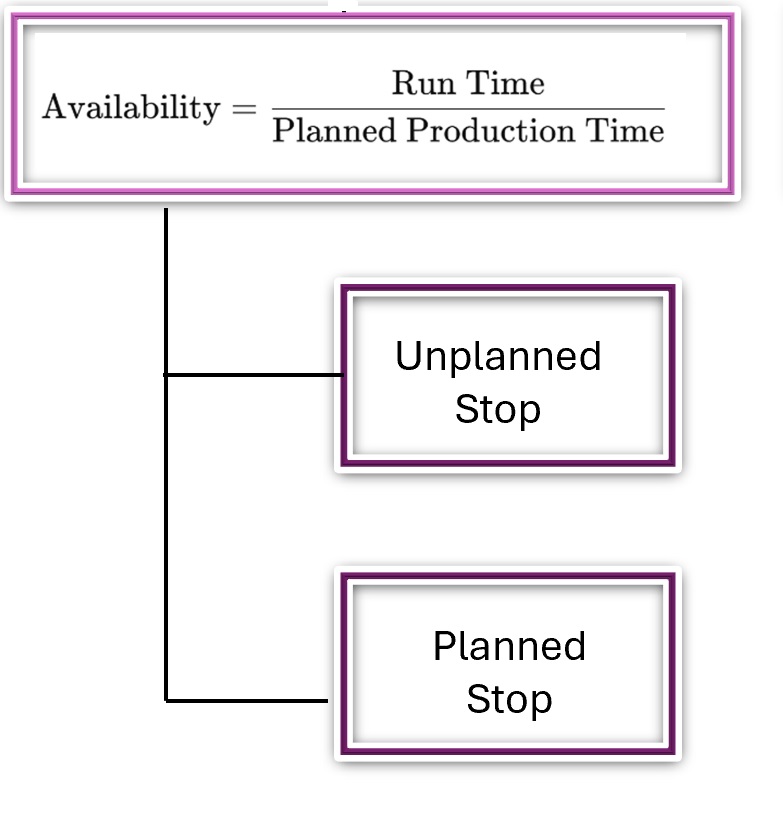
Availability Losses
1. Unplanned Stops
Ever wonder why your machine suddenly stops, throwing production off course? That is a breakdown, one of the six major losses. Unplanned stoppages caused by breakdowns, equipment failure, power outages, sensor failures, or operator errors causing machine stoppage. They do not just halt production—they waste time, incur costly repairs, and disrupt deadlines. For example, if a machine is scheduled to run for six hours but only operates for four due to unexpected failures, the two hours of downtime represent a significant loss.
How can you combat this? Prevention is key. Strategies like preventive maintenance, predictive maintenance, and root cause analysis can dramatically reduce the occurrence of breakdowns, keeping your production on track and minimizing costly disruptions.
2. Planned Stops (Setup and Adjustments)
Do you find time slipping away during product changeovers or machine adjustments? Planned stops, like setups and adjustments, are another major loss in manufacturing. This category includes time lost during product changeovers, tool replacements or adjustments, machine warm-ups, cleaning procedures, routine maintenance checks, quality inspections, or recalibrations. While these may seem unavoidable, every second spent tweaking or troubleshooting settings chips away at productivity, creating hidden downtime that adds up over time.
How do you address this? One effective method is implementing the Single-Minute Exchange of Dies (SMED) technique, a lean manufacturing process aimed at minimizing changeover time. The goal of SMED is to perform as many steps as possible while the machine is running. Additionally, standardizing procedures and training your team to minimize trial-and-error adjustments can significantly streamline setups, ensuring faster and more efficient production transitions.
By identifying and addressing these Availability losses, manufacturers can reduce downtime, improve efficiency, and move closer to achieving their OEE goals.
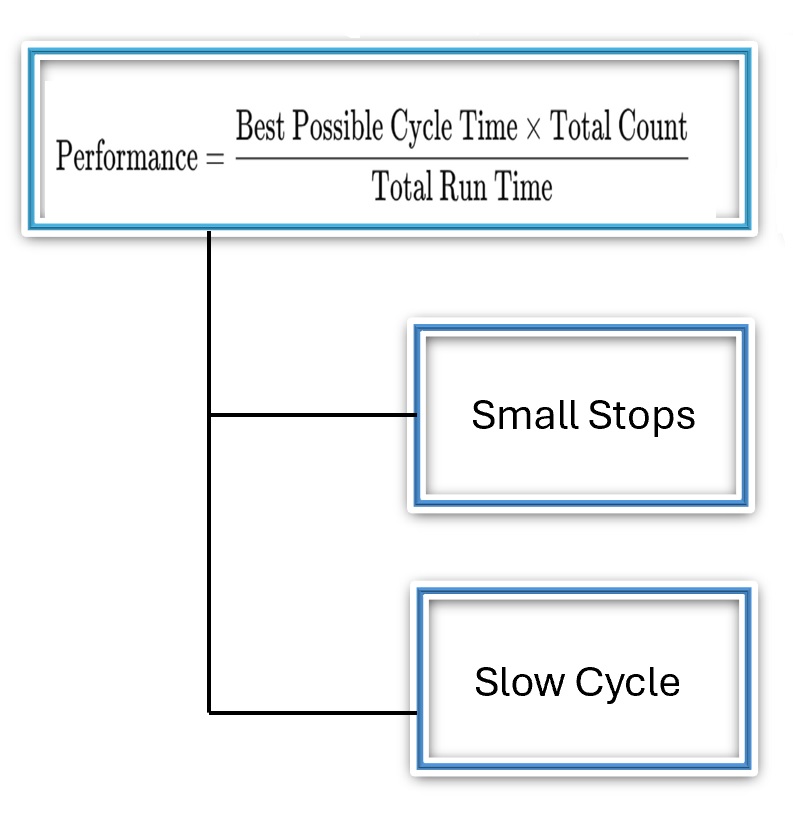
Performance Losses
3. Small Stops
Are small delays quietly sabotaging your production efficiency? Let’s talk about small stops, the third major loss in manufacturing. These are short, unplanned interruptions caused by issues like a sensor misfire, a jammed part, or a minor equipment glitch. Often referred to as idling and minor stops, these events typically last just a minute or two and are usually resolved quickly by the operator.
Although small stops don’t trigger alarms, they chip away at productivity by stealing valuable seconds, adding up over time, and hurting overall efficiency. The real challenge is that these issues are often chronic, causing operators to overlook their cumulative impact.
So, how do you tackle small stops? Here are a few strategies:
– Optimize equipment settings to prevent recurring interruptions.
– Train operators regularly to quickly identify and address potential issues.
– Use root cause analysis to pinpoint and eliminate the underlying problems behind recurring small stops.
By proactively addressing small stops, you can reclaim lost time and significantly improve your production efficiency.
4. Slow Cycle
Is your equipment running slower than it’s designed to? Slow cycles or reduced speed represent the fourth major loss in manufacturing. This occurs when a machine operates below its ideal speed, leading to performance losses. Common causes include worn-out components, poor lubrication, suboptimal settings, dirt accumulation, substandard materials, harsh environmental conditions, or operator inexperience.
Addressing reduced speed requires a proactive approach. Here are some strategies to tackle the issue:
– Perform regular maintenance to keep machines in optimal condition.
– Fine-tune operations to align with the machine’s ideal speed settings.
– Use tools like InsightView to identify bottlenecks and optimize performance.
For more information on InsightView, check out the blog section below or request a trial account here to see how it can help boost your equipment’s performance.
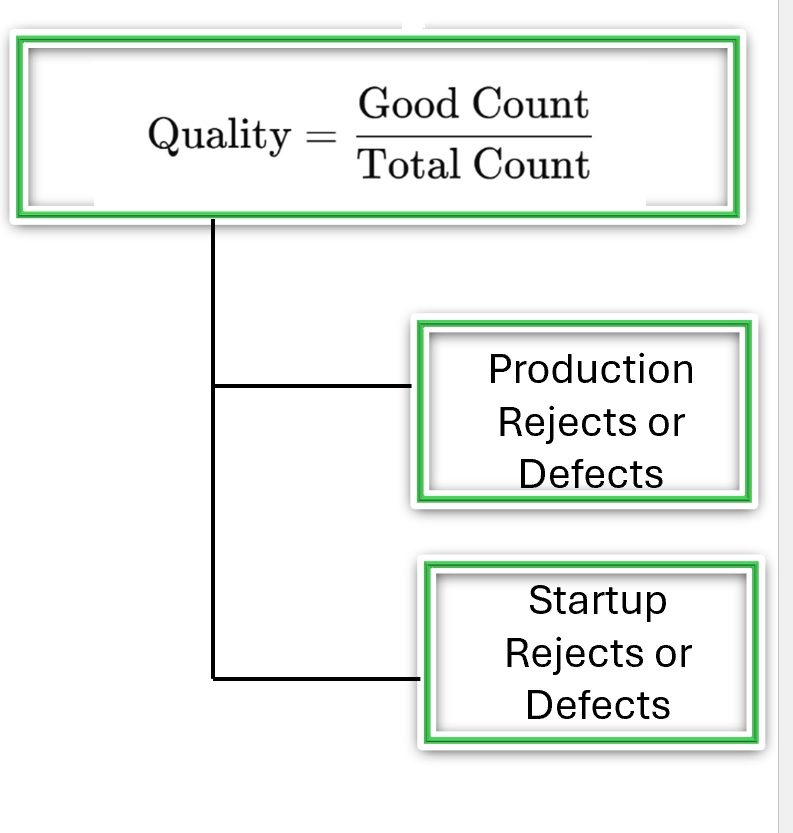
Quality Losses
5. Reduced Yields (Startup Rejects or Defects)
Have you noticed defects appearing right after starting a machine? These startup rejects represent the fifth major loss in manufacturing. Startup losses occur when parts are scrapped or require rework immediately following equipment startup, production line resets, or maintenance activities. Even if a defective part is reworked to meet quality standards, it is still considered a production reject in OEE calculations because the additional effort reflects a loss of efficiency.
Startup defects often result from improper settings, inadequate warm-up, or operator errors. While they might seem minor at first, these early-stage defects waste valuable materials, time, and resources. Over time, the cumulative costs associated with poor quality due to reduced yields can significantly affect production efficiency. In OEE calculations, these losses directly impact the quality factor, which measures the percentage of good parts produced versus total production output.
To minimize startup losses and improve yields, consider these strategies:
– Conduct thorough pre-startup checks to ensure the equipment is fully prepared for smooth operation.
– Standardize machine settings to reduce variability and prevent setup errors.
– Train operators to handle startups effectively and quickly address potential issues.
By addressing startup rejects proactively, you can reduce waste, boost production quality, and drive higher overall efficiency in your manufacturing processes.
6. Production Rejects: The Sixth Major Loss in Manufacturing
Are defective products sneaking into your production process? Production rejects represent the sixth major loss in manufacturing. They occur when defective parts are produced during stable, steady-state operations. Equipment wear, material issues, process variability, or operator skill levels often cause these defects.
Production rejects can result in total scrap or require rework. Every scrapped part wastes time, materials, and energy—and worse, it can erode customer trust if defective products make it past quality control. Even when defective parts are reworked to meet standards, they are still counted as production rejects in OEE calculations because they deviate from the goal of producing perfect parts “right the first time.” A higher number of production defects directly lowers the OEE quality score by reducing the percentage of good units produced.
To minimize production rejects, consider these strategies:
– Implement automated quality checkpoints in multi-stage production systems to detect issues early.
– Use Root Cause Analysis to identify and eliminate recurring defects.
– Apply mistake-proofing techniques (poka-yoke) to prevent errors from occurring.
– Leverage tools like InsightView to effectively detect root causes and monitor quality trends. To request a temporary account to try InsightView, please click here.
Proactively addressing production rejects can reduce waste, improve product quality, and boost your overall OEE, ensuring a more efficient and reliable manufacturing process.
Leveraging TPM, OEE, and Advanced Tools to Tackle the Six Big Losses
TPM and OEE are essential in addressing the Six Big Losses in Manufacturing. With tools like InsightView, identifying and analyzing these losses becomes far more efficient. By enabling a thorough analysis of your production process, InsightView qualifies each loss, empowering you to take data-driven action. Prioritizing this type of analysis simplifies the process of pinpointing and resolving inefficiencies effectively.
In addition, advanced solutions like KnowledgeView take it further by offering predictive maintenance capabilities. These tools leverage sensors and advanced algorithms to anticipate issues before they occur, improving OEE and reducing costly downtime. By integrating tools like InsightView and KnowledgeView into your operations, manufacturers can unlock data-driven insights into performance and losses that were previously inaccessible. These technologies enable faster, more comprehensive insights and help prioritize the most impactful issues for resolution, driving significant cost and time savings.
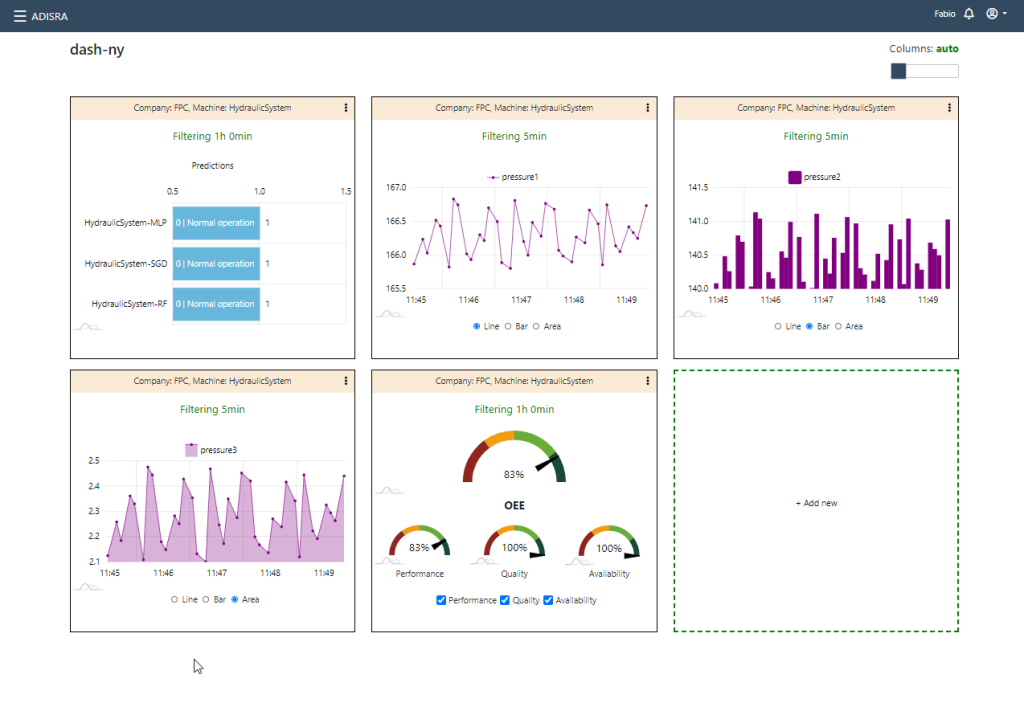
Why Performance Management Solutions Matter
Performance management solutions can transform your OEE initiatives by uncovering unplanned downtime, categorizing it, and highlighting the most impactful opportunities to improve productivity and reduce costs.
Regaining lost production time can lead to revenue increases, making performance optimization a critical investment.
InsightView provides a powerful, intuitive platform for analyzing productivity across machines and processes. Covering essential metrics like OEE and the Six Big Losses, it offers:
– Customizable dashboards tailored to your specific operational needs.
– A cloud-based SaaS model designed for mid-market manufacturers, enabling advanced analytics across machines, lines, or plants.
– Minimal IT costs and fast deployment, with regular updates included in the service fee.
KnowledgeView focuses on predictive maintenance, helping manufacturers maximize machine uptime and reduce scheduled maintenance costs. Key benefits include:
– Predictive algorithms to anticipate issues and prevent unplanned disruptions.
– Extended equipment lifespan by minimizing wear and tear through timely interventions.
– A SaaS delivery model with reduced IT overhead and continuous feature updates, ensuring seamless maintenance management.
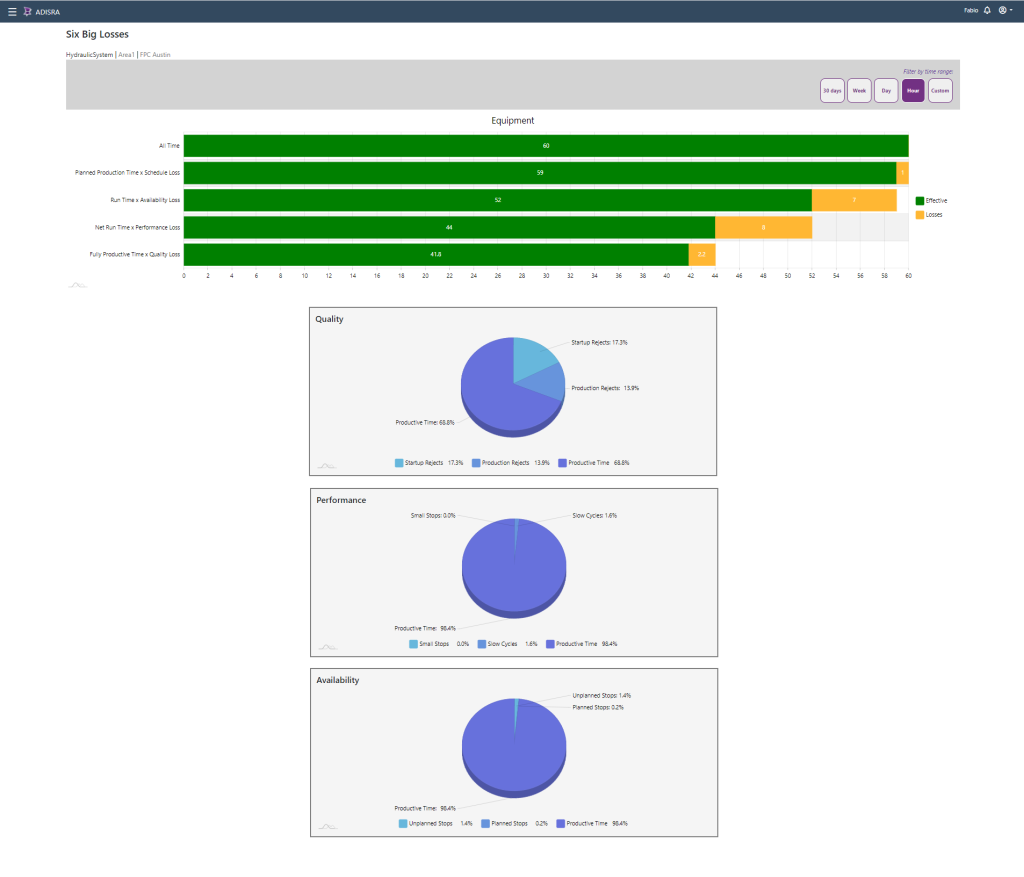
Mobile Access for Greater Flexibility
All ADISRA products, including InsightView and KnowledgeView, are accessible on desktops, industrial panels, and mobile devices. This flexibility allows operators and managers to:
– Monitor equipment performance.
– Receive real-time alerts.
– Access OEE insights and predictive analytics anytime, anywhere.
This mobility enables faster decision-making and more responsive operations, empowering manufacturers to avoid potential issues.
Experience InsightView and KnowledgeView for Yourself
Ready to improve your OEE and maintenance management? Visit our website to request a temporary account here and explore how InsightView and KnowledgeView can aid your digital transformation journey.
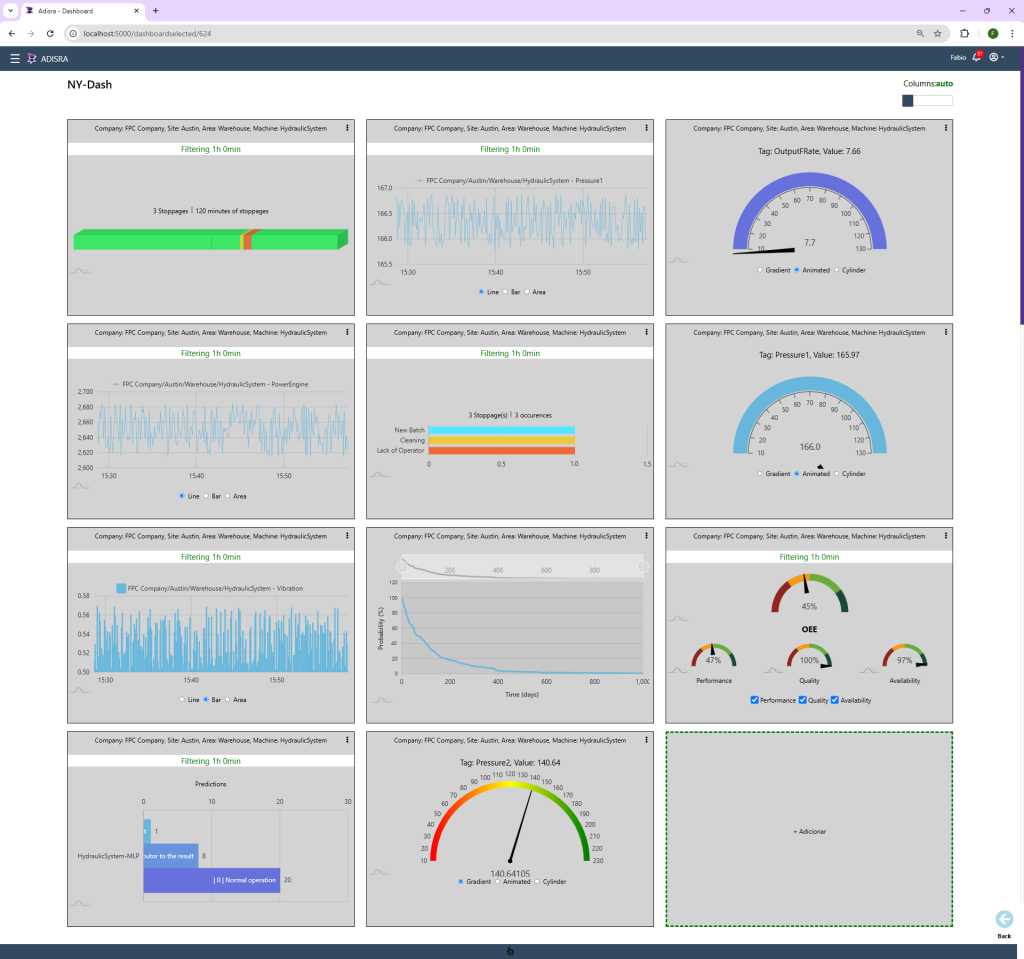
ADISRA®, ADISRA’s logo, InsightView®, and KnowledgeView® are registered trademarks of ADISRA, LLC.
© 2025 ADISRA, LLC. All Rights Reserved.