
Last week, we explored the Six Big Losses and their impact on production line efficiency and productivity. There is a critical intersection between energy efficiency and productivity, however, that manufacturers cannot overlook.
Rising energy costs and regulatory challenges in today’s environment can heavily impact a company’s bottom line—and consumers, suppliers, and vendors increasingly demand sustainably produced goods—manufacturers are rethinking how they measure and optimize energy consumption. Manufacturers can lower costs, shrink their environmental footprint, and boost productivity by refining equipment and processes to consume less energy. Energy efficiency goes beyond mere conservation—it fosters a more streamlined, cost-effective, and sustainable operation throughout the manufacturing process.
Tackling our energy challenges requires more than just focusing on generation—we must also rethink how we consume energy. With the demand for computational power accelerating due to the widespread adoption of cloud computing and generative AI, optimizing energy usage in data centers has become a pressing concern.
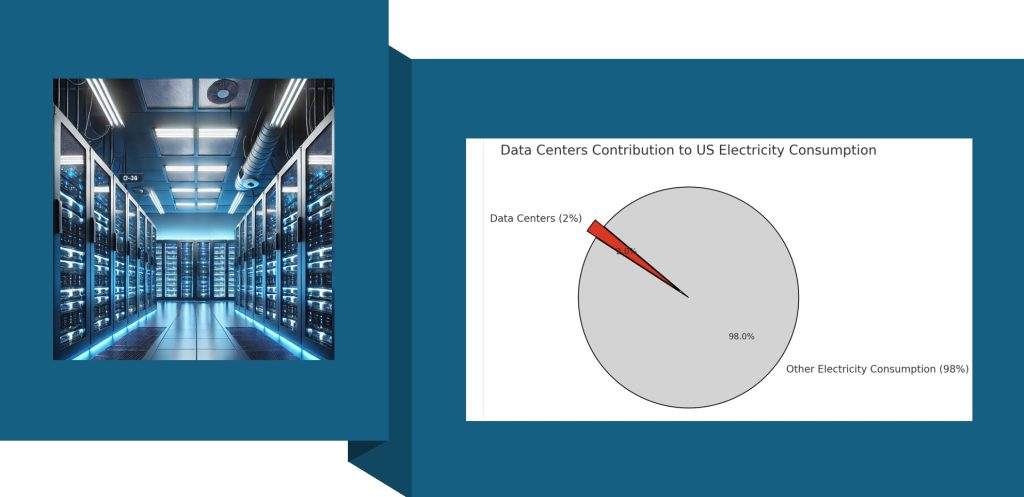
Data centers are among the most energy-intensive facilities, consuming 10 to 50 times more energy per square foot than a typical commercial office. According to the U.S. Department of Energy, they collectively account for approximately 2% of total U.S. electricity consumption. As the nation’s dependence on information technology continues to grow, data center and server energy use is projected to increase, underscoring the urgent need for improved energy efficiency.
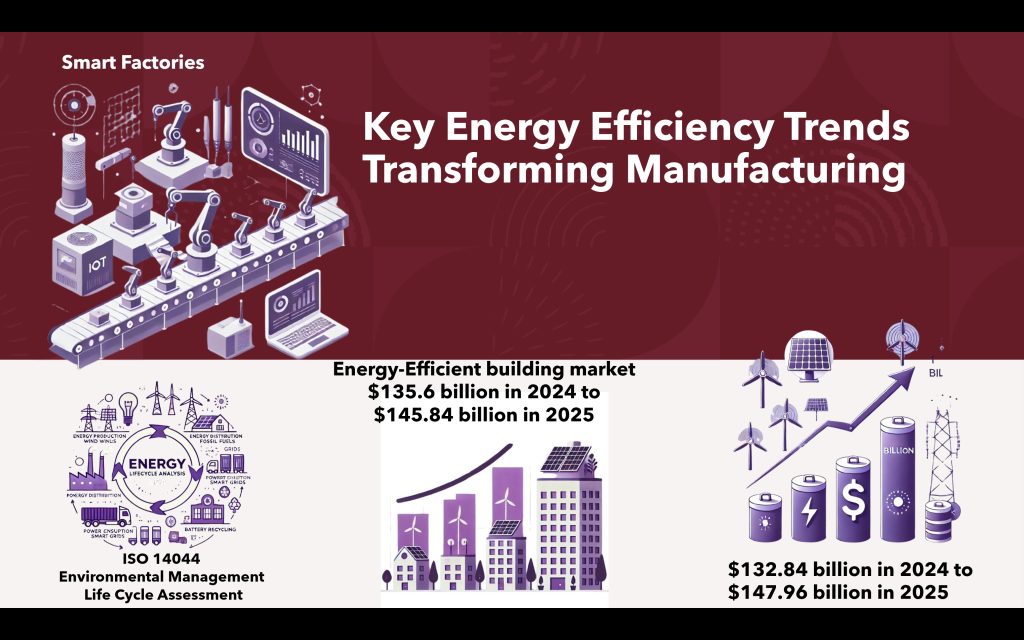
Key Energy Efficiency Trends Transforming Manufacturing
Beyond cost savings and regulatory requirements, several market trends are driving the growing emphasis on energy management. These include:
Smart Factories – Smart factories are at the core of the energy efficiency revolution in manufacturing. Picture a facility where every piece of equipment—robots, sensors, and production systems—continuously communicates, analyzes data, and adjusts operations in real-time to optimize energy consumption. After a period of significant industry shifts, smart manufacturing technology remains a leading trend for 2025, as manufacturers seek innovative ways to enhance processes, improve efficiency, and build resilience against disruptions and unpredictable challenges.
According to the Business Research Group, the smart factory market is expected to grow from $82.07 billion in 2024 to $89.56 billion in 2025, reflecting a compound annual growth rate (CAGR) of 9.1%.
Renewable Energy Sources—Renewable energy integration is revolutionizing manufacturing by incorporating sustainable sources like solar and wind power into existing energy systems. This transition reduces reliance on fossil fuels, paving the way for cleaner and more efficient operations.
According to the Business Research Group, the renewable energy integration systems market is projected to grow from $132.84 billion in 2024 to $147.96 billion in 2025, reflecting a compound annual growth rate (CAGR) of 11.4%. As manufacturers strive for sustainability and energy resilience, renewable energy adoption is a game-changer for the industry.
Energy-Efficient Equipment – Energy-efficient equipment in manufacturing is designed to perform the same tasks as traditional machinery but with significantly lower energy consumption. By leveraging advanced technologies and optimized designs, these innovations enable manufacturers to maintain productivity while reducing their energy footprint and operational costs.
One key area of energy-efficient equipment is building automation, which includes high-efficiency HVAC systems, lighting, building controls, and water management solutions. These technologies enhance energy conservation in industrial facilities, contributing to long-term cost savings and sustainability.
According to The Business Research Company, the energy-efficient building market is experiencing strong growth, projected to expand from $135.6 billion in 2024 to $145.84 billion in 2025, with a compound annual growth rate (CAGR) of 6.0%, reaching $184.19 billion by 2029. This trend underscores the growing commitment to energy efficiency across industries.
Lifecycle Analysis (LCA) – LCA is a systematic approach to evaluating a product’s environmental impact throughout its entire lifecycle—from raw material extraction and manufacturing to usage and disposal. By analyzing each stage, companies can pinpoint areas for improvement and create more sustainable products while gaining a comprehensive understanding of their environmental footprint.
For guidance on LCA, the ISO 14044 standard—Environmental Management – Life Cycle Assessment – Requirements and Guidelines—provides essential requirements and best practices. You can access the guidelines here.
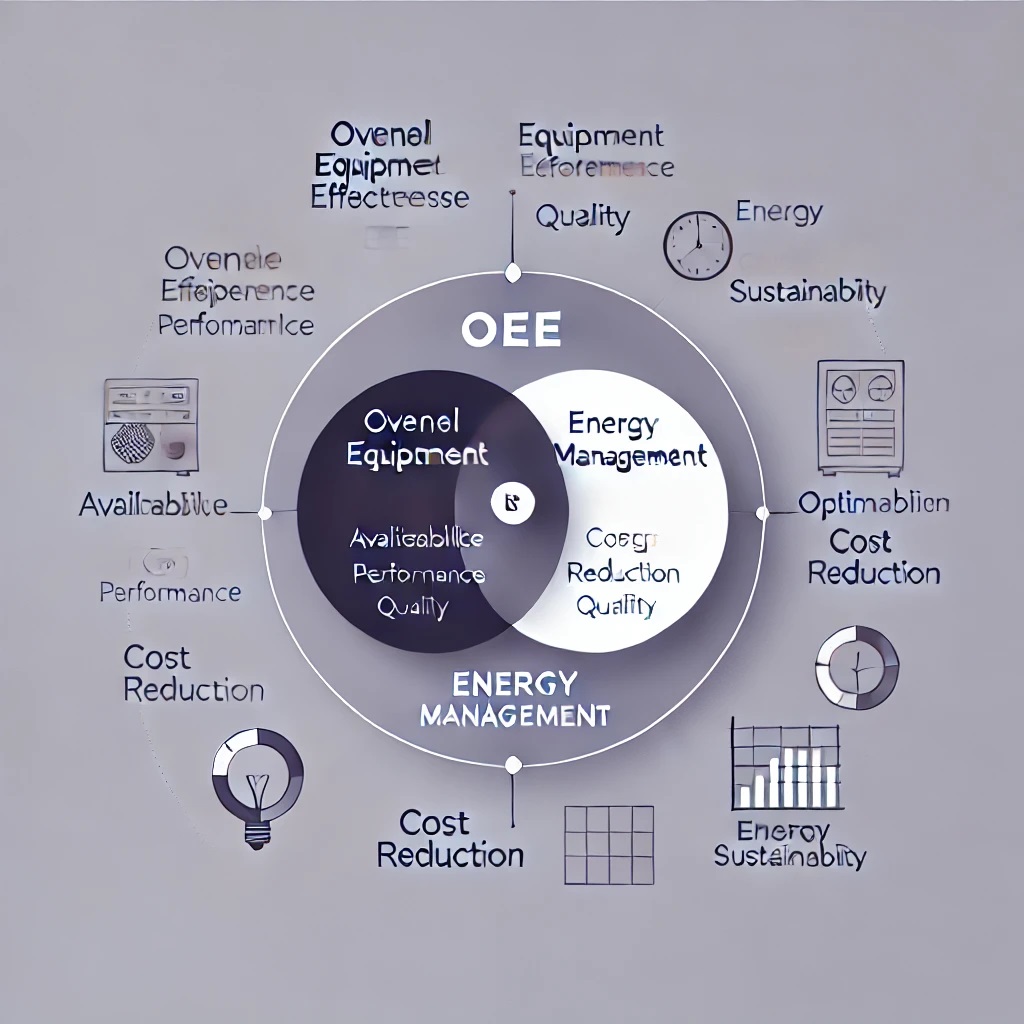
The Relationship Between OEE and Energy Management
Overall Equipment Effectiveness (OEE) and energy management are closely linked, with improvements in one often driving enhancements in the other. In previous blogs, which you can read here, we have explored how OEE measures productivity through three key factors:
Availability – The percentage of time equipment is operational.
Performance – The speed at which equipment runs relative to its designed capacity.
Quality – The percentage of defect-free products produced.
How Energy Management Impacts OEE
Availability: Power failures and energy inefficiencies cause unplanned downtime. A robust energy management system minimizes disruptions, improving equipment uptime.
Performance: Machines running at optimal energy levels operate more efficiently, reducing cycle times and increasing throughput. Addressing energy inefficiencies helps sustain peak performance.
Quality: Energy fluctuations affect production accuracy, leading to defects. A stable energy supply ensures consistent product quality, reducing rework and waste.
Energy management optimizes and reduces energy consumption, leading to cost savings and environmental benefits. The connection between OEE and energy management lies in efficiency—inefficient equipment consumes more energy and suffers from more downtime, slower performance, and higher defect rates. By integrating energy management strategies, manufacturers can improve OEE, lower costs, and enhance sustainability.
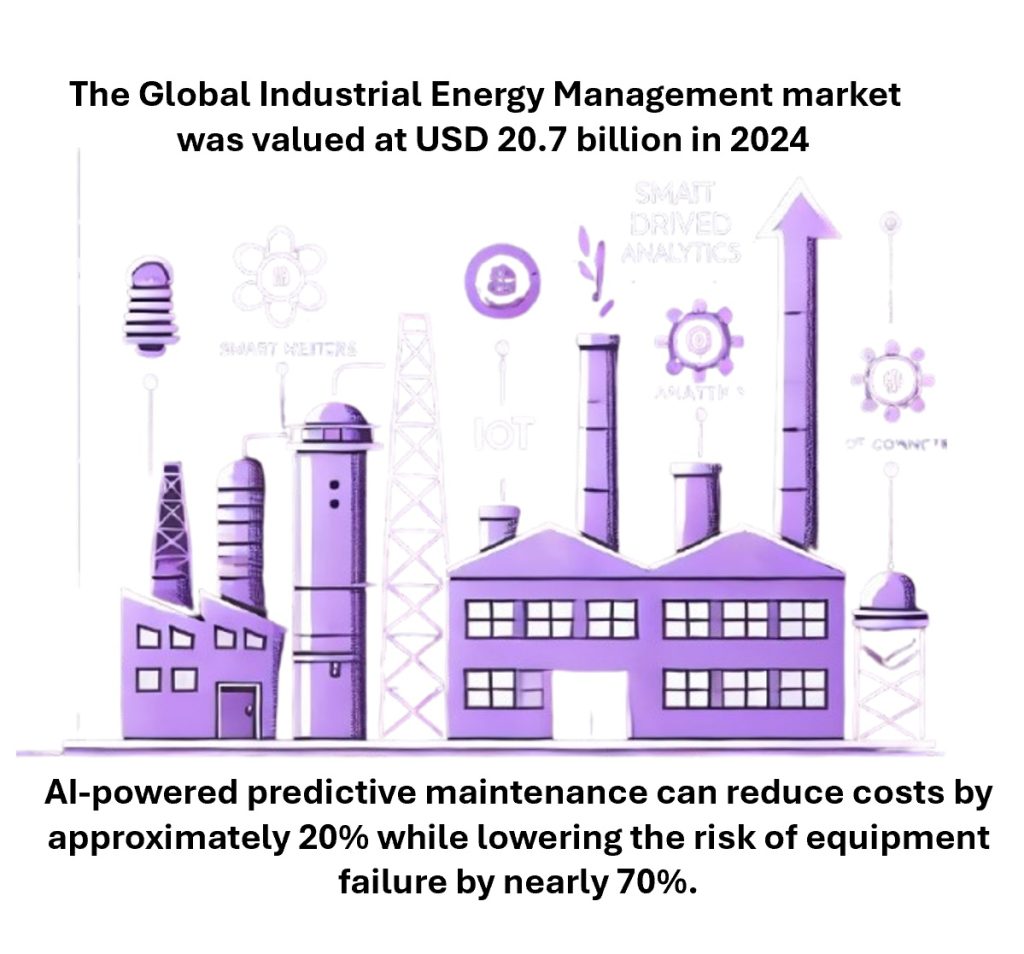
Optimizing Industrial Energy Management
The Industrial Energy Management System (IEMS) market is poised for significant growth in the coming years. Designed to optimize energy consumption in industrial environments, IEMS plays a critical role in reducing operational costs, minimizing energy waste, and supporting sustainability initiatives. According to Global Market Insights, the global industrial energy management market was valued at USD 20.7 billion in 2024.
A key driver of this growth is the increasing integration of IoT devices and artificial intelligence (AI), enabling real-time monitoring, data-driven analysis, and automated energy management. These advancements enhance decision-making efficiency and drive substantial cost savings. The U.S. Department of Energy Data Maintenance estimates that AI-powered predictive maintenance can reduce costs by approximately 20% while lowering the risk of equipment failure by nearly 70%. Additionally, AI-driven anomaly detection and energy optimization are expected to improve energy efficiency by 10-15%, leading to more sustainable and cost-effective industrial operations.
ADISRA InsightView and Its Energy Management Module
InsightView offers an intuitive solution for analyzing productivity data across machines and processes, providing key insights into metrics such as OEE and the Six Big Losses. With customizable dashboards, users can tailor their monitoring experience to meet specific operational needs.
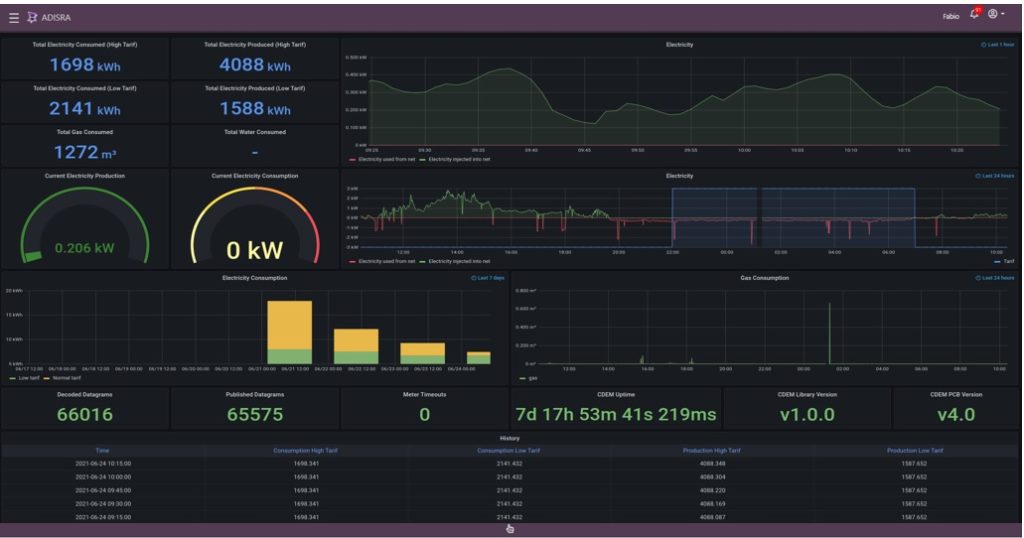
Designed for mid-market manufacturers, InsightView’s cloud-based model delivers advanced analytics and comparative insights across machines, production lines, or entire facilities. As a software-as-a-service (SaaS) solution, it reduces IT costs and accelerates deployment with minimal configuration. Regular updates are included in the subscription, ensuring users always have access to the latest features and enhancements.
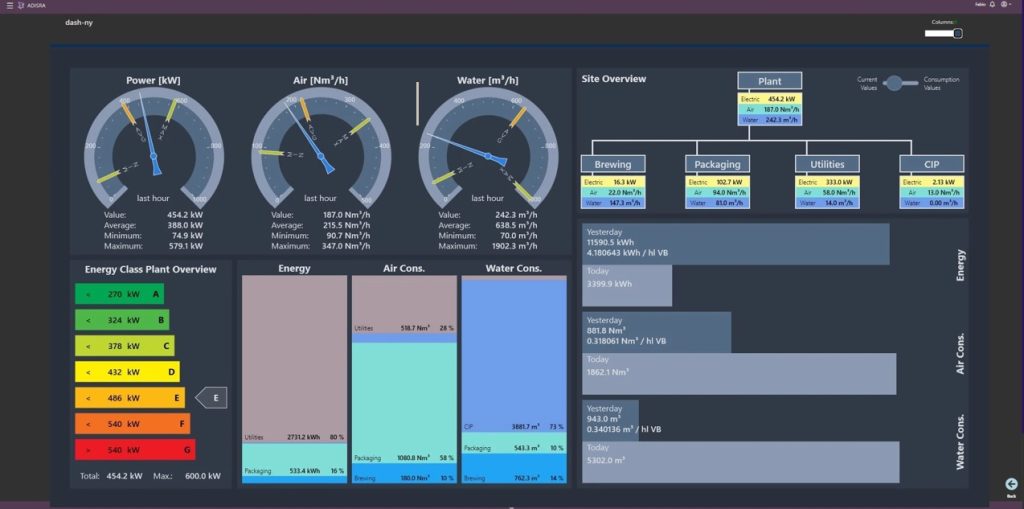
InsightView includes a powerful energy management dashboard designed to enhance operational efficiency by optimizing machine operating times based on actual demand. It enables the strategic scheduling of energy-intensive processes during off-peak hours, helping to reduce operating costs while lowering environmental impact. By aligning energy usage with production efficiency, InsightView supports sustainability initiatives by minimizing overall energy consumption and reducing the carbon footprint.
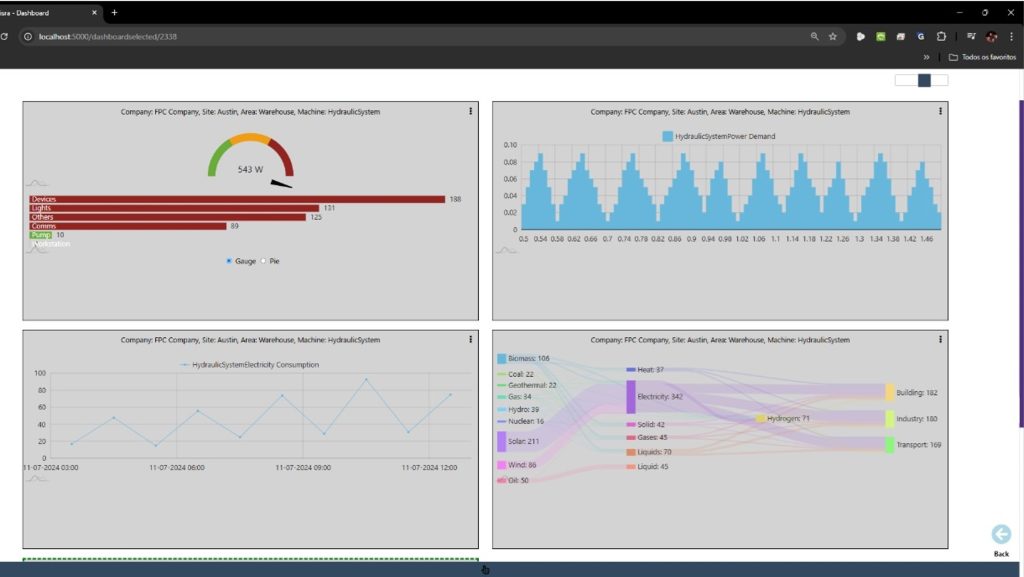
Additionally, InsightView collects, measures, and analyzes energy consumption data from various sources, including electricity, gas, water, and other energy inputs. With both real-time and historical insights, it helps identify usage patterns, detect anomalies, and uncover opportunities for energy conservation, enabling smarter, data-driven decision-making for industrial energy management.
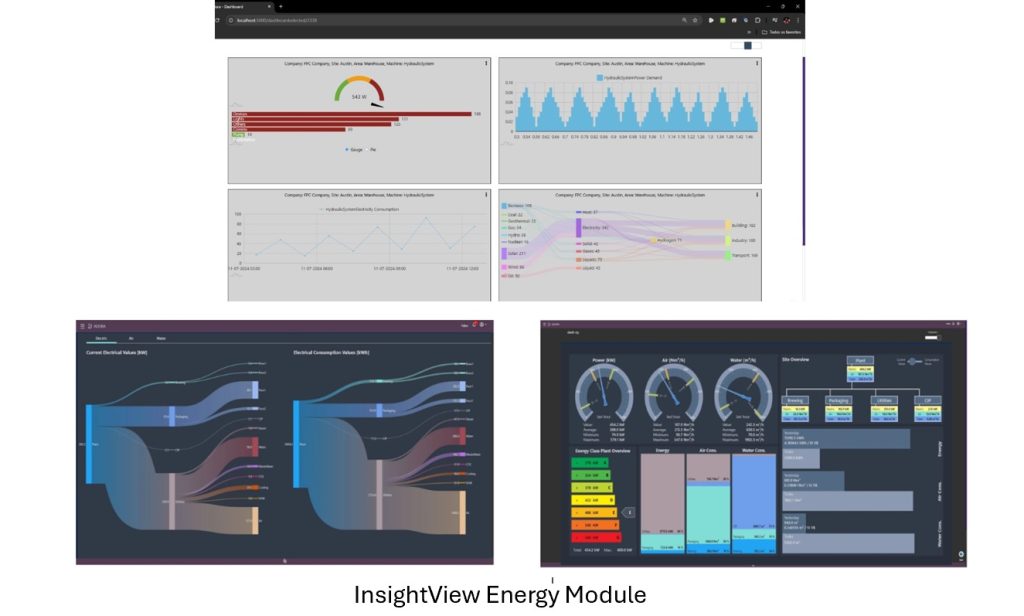
Want to experience InsightView firsthand? Request a temporary account on our website today!
Rising power demand and growing climate concerns are reshaping how energy is generated, stored, and consumed. The expansion of nuclear power and the continued growth of renewable energy are setting the stage for an energy infrastructure that fosters innovation rather than limiting progress.
Effective energy management is a key driver of operational excellence, playing a crucial role in optimizing OEE and overall productivity. By leveraging real-time energy monitoring, predictive analytics, and proactive maintenance, manufacturers can minimize waste, enhance efficiency, and improve product quality. As industrial automation continues to evolve, businesses that prioritize energy efficiency will not only reduce costs but also gain a competitive edge while advancing long-term sustainability goals.
Conclusion
As industries face rising energy costs, regulatory pressures, and increasing demands for sustainability, effective energy management has become a fundamental pillar of operational success. The integration of smart technologies—such as IoT-driven monitoring, AI-powered analytics, and predictive maintenance—is transforming how manufacturers optimize energy consumption while improving productivity and reducing costs.
The connection between energy efficiency and OEE is undeniable: minimizing energy waste leads to fewer disruptions, better performance, and higher-quality outputs. By adopting advanced energy management strategies, businesses can achieve greater operational resilience, enhanced sustainability, and a competitive edge in an increasingly demanding industrial landscape.
Manufacturers that embrace energy management solutions, such as ADISRA InsightView, will be well-positioned to navigate the evolving energy landscape. By leveraging real-time insights and automation, they can not only reduce costs and carbon footprints but also drive long-term innovation and efficiency. Now is the time to invest in smarter, more sustainable energy management practices—because the future of manufacturing depends on it.